Manufacturers are doubling down on their efforts to reduce costs and improve the performance and safety of the battery technology that underpins these vehicles.
While much has been written about the impressive advances in Li-ion battery chemistries, original equipment manufacturers (OEMs) also pay close attention to the selection of the appropriate battery cell format, also referred to as the ‘form factor.’
The importance of the form factor extends beyond mere space and packaging requirements. Indeed, the technical fit alone is usually not the primary consideration. OEMs are increasingly aligning, and adapting, the choice of form factor with their strategic and performance objectives, whether it be high energy density for increased range, or safe and durable extreme fast charging.
By selecting an appropriate form factor OEMs can optimize functionality to suite their design objectives: For instance a manufacturer may wish to optimize the fast charging capability of its EVs.
StoreDot's proprietary 100inX cell technology is cell form-factor agnostic. Due to the combined properties of its unique electrode design, specialized electrolyte and advanced electrode materials any format can benefit from the fast-charging capabilities of XFC. This empowers OEMs to choose the format that best suits their vehicle design, manufacturing platform capabilities, and market segment without sacrificing charging speed.
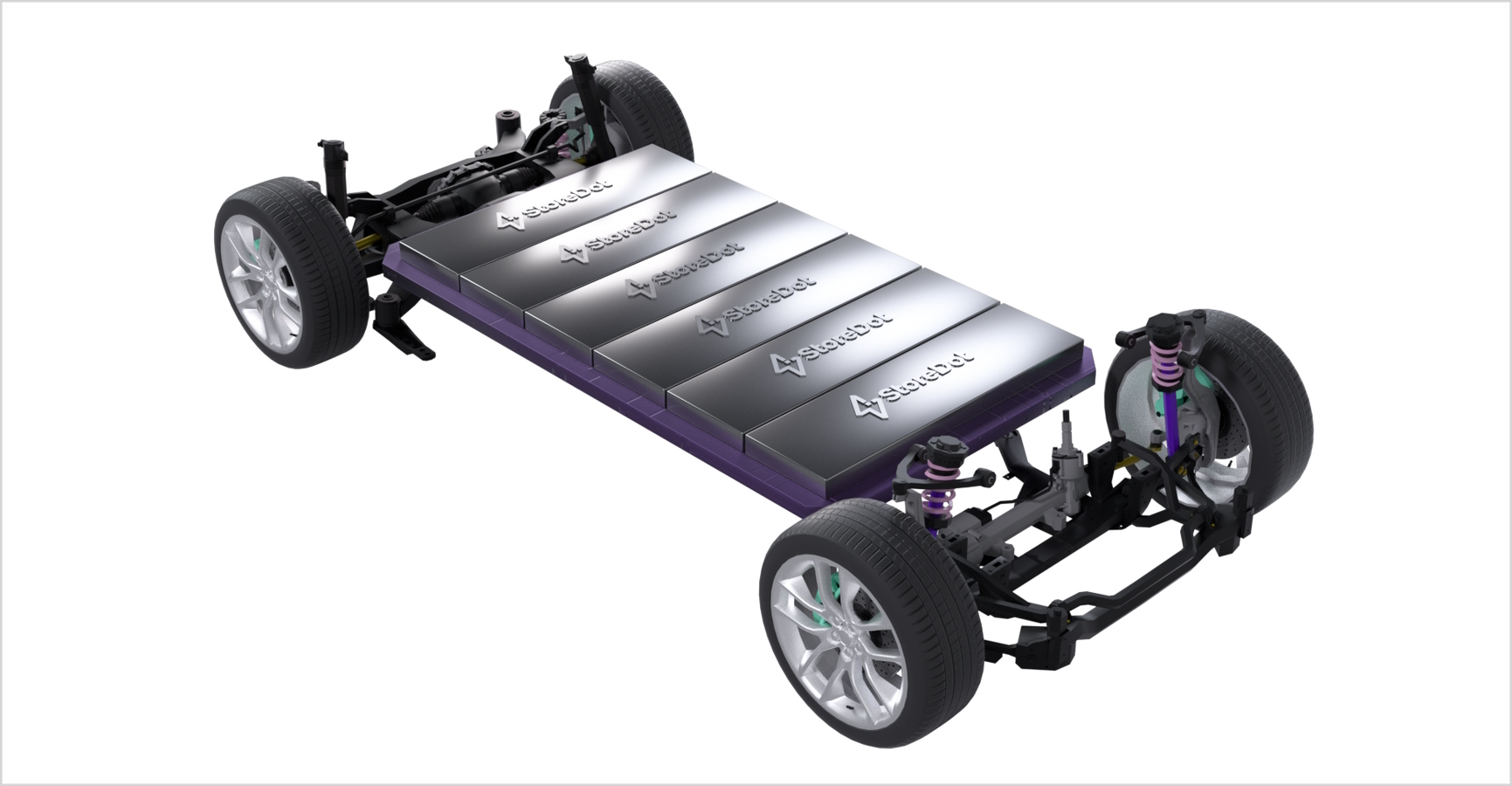
Currently, three cell form factors dominate the EV market: prismatic, pouch, and cylindrical formats. Each type brings its own set of advantages and disadvantages, allowing OEMs to customize their EV battery packs to align with their product strategies.
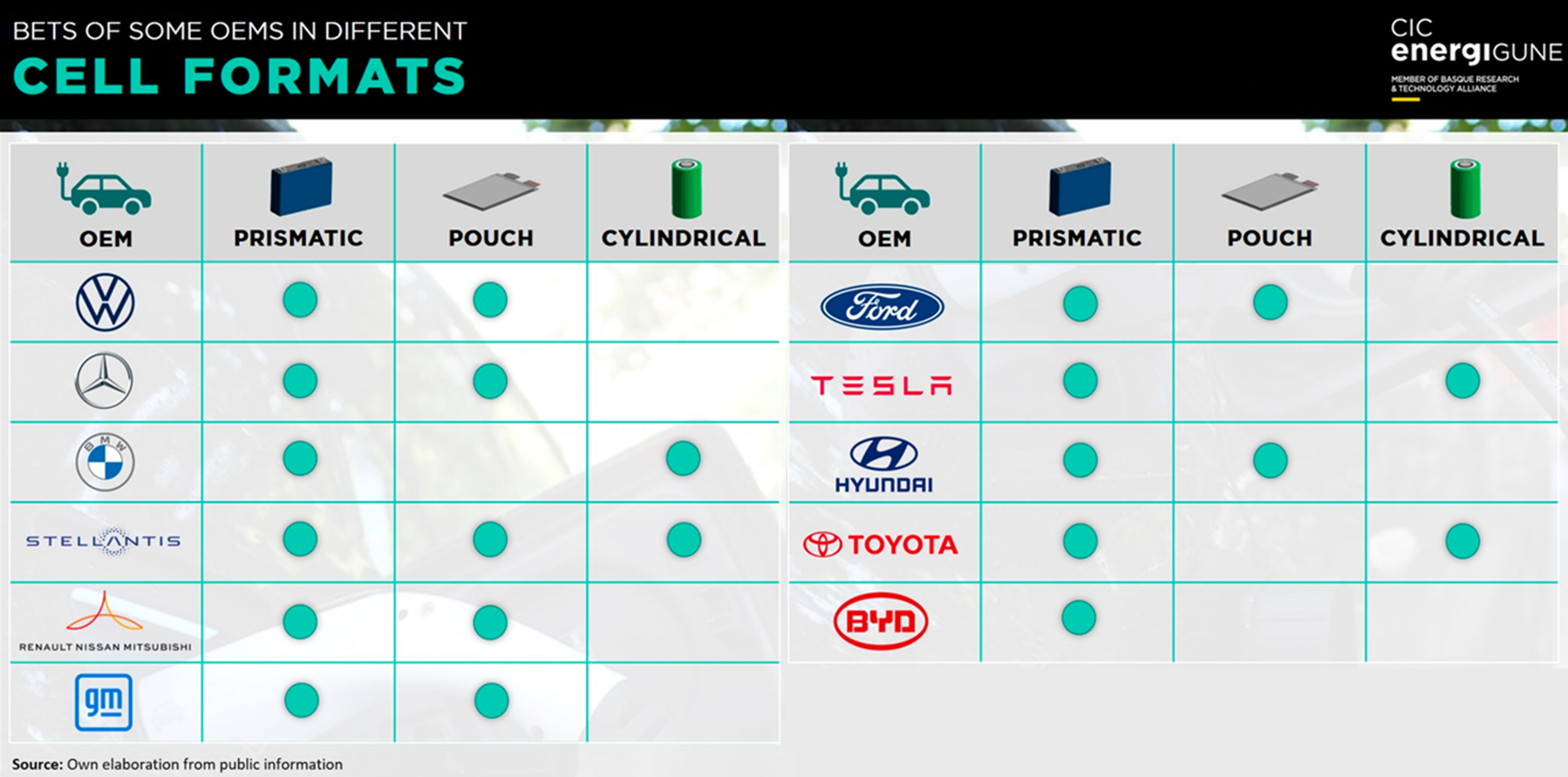
In 2020, the market share of each format across the 6 largest battery manufacturers was: prismatic ~40 percent, pouch ~35 percent, and cylindrical ~15 percent.
Selecting the best of these cell formats for the application is often the key to enabling an OEM to fulfill the functional objectives of its EV strategies.
Battery cell formats play a vital role in enabling OEMs to fulfill their strategies
When deciding on a Li-ion EV battery specification, OEMs have to carefully consider all the interrelated factors, including the strengths and weaknesses of each battery cell form factor in meeting the company’s strategies for the particular model being designed.
The important contribution of the battery-cell form factor in meeting a company’s wider strategy is well illustrated by Tesla’s switch from cylindrical to prismatic cells in all its standard-range Model 3s and Ys. To reduce the cost of its Standard Range lineup Tesla chose to change to lithium iron phosphate (also known as LFP or LiFePO4) battery chemistry, which is also less energy-dense than the nickel cobalt aluminum (NCA) chemistry used in its cylindrical cells. By converting to larger format, higher capacity, prismatic cells – which also allowed the company to embrace cell-to-pack (CTP) design - Tesla was able to partially compensate for the loss in energy density, while retaining the cost benefits.
Tesla’s original choice of the cylindrical cell was primarily driven by availability, safety, and cost. As the oldest form factor, the greatest advantage of the cylindrical cell is its availability and cost-effective manufacturing – thanks largely to economies of scale.
Cylindrical cells, because of their shape (with a beneficial surface area to volume ratio) that allows for cooling pathways between the cells, also have good thermal performance when assembled into packs.
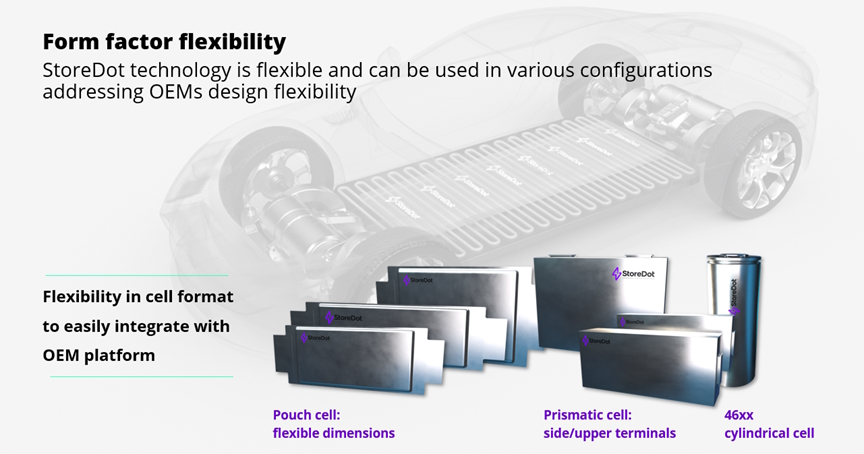
However, there are also drawbacks to the cylindrical format. Due to their shape, battery pack volumetric efficiency is compromised. The gravimetric energy density, at a pack level, is also lower than that of pouch or prismatic formats - thereby affecting applications with strict weight constraints or range requirements.
Additionally, OEMs need to plan for a much higher cell count, compared to prismatic cells, to achieve the same capacity. Even with a 4680 with ~25 Ah capacity, as presented by Tesla, the cell count is 4 times that of a 100 Ah prismatic cell to achieve the same pack capacity, which in turn increases the overheads for BMS, TMS, etc.
Due to these limitations, many in the industry believe cylindrical cells have reached their ceiling in terms of performance and optimization, paving the way for pouch and prismatic formats to dominate future strategies.
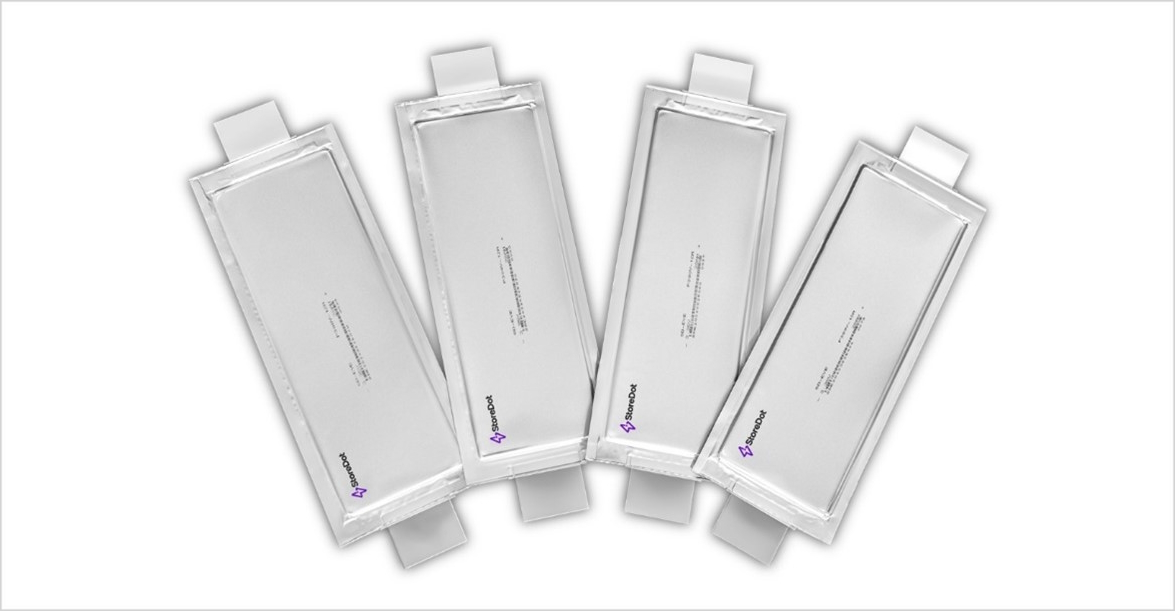
The pouch cell, although not as widely used in EV applications as the prismatic format, has two characteristics that OEMs can leverage to customize their EV strategies: Weight and flexible packaging.
Because of its construction the pouch cell is flexible, allowing designers to create custom shapes and sizes to fit specific applications. In terms of space optimization, this translates to between 90 to 95 percent packaging efficiency which converts into improved volumetric energy densities. The absence of a rigid casing also contributes to its light weight, making the pouch cell suitable for applications with weight constraints – although this is often offset to some extent by the weight of the battery-pack housing.
One of the critical challenges for OEMs is battery thermal management. Efficient heat dissipation is essential to maintain optimal battery performance, extend battery life, and ensure the safety of the vehicle during fast charging. The downside of pouch cells in EV applications is the poor thermal conductivity of the pouch.
Thus, in applications where thermal management is deemed critical, manufacturers turn to cylindrical cells or increasingly, the prismatic form factor.
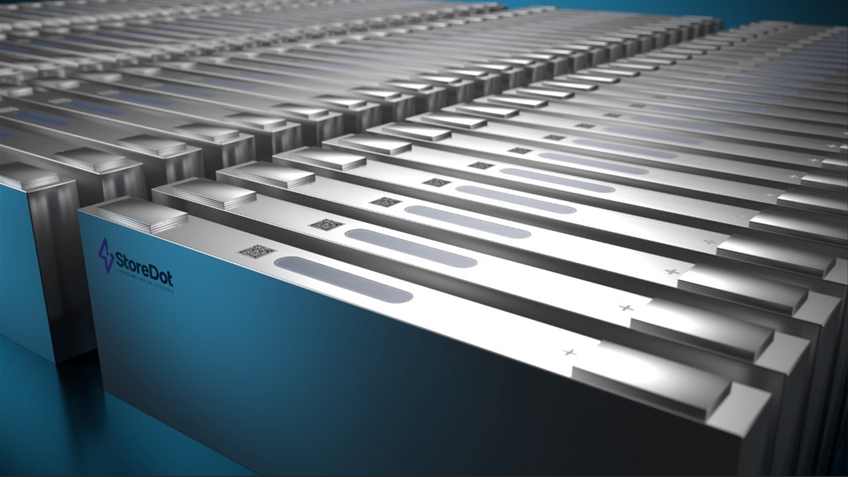
Prismatic cells that, thanks to their stacked "layer" configuration, facilitate heat dissipation and temperature regulation also offer excellent space utilization. The stacked design allows OEMs to maximize the available volume within the vehicle, thereby optimizing the energy density which in turn allows the OEM to either increase the EV’s range or reduce the size of the battery for the same performance depending on the OEM’s strategy.
Looking for innovative ways to increase energy density and range, several OEMs are turning to large format prismatic cells, assembled directly into the battery pack, in the CTP format. By foregoing the traditional assembly of cells into modules, weight is reduced and volume utilization optimized – resulting in cost savings and improvements in energy density.
StoreDot’s innovative concept gives OEMs access to a cost-effective extreme fast charging EV strategy
Power density is another critical parameter that OEMs evaluate when selecting a Li-ion battery cell form factor. Higher power density enhances fast charging capabilities and EV dynamic performance, such as acceleration.
Whereas typical cell-to-pack architectures aim to improve energy density to extend range, StoreDot also enables extreme fast charging (XFC) with its I-BEAM XFC™ concept. It overcomes many of the complexities and cost challenges of embedding XFC capability at the vehicle level, allowing OEMs to more easily implement fast charging strategies.
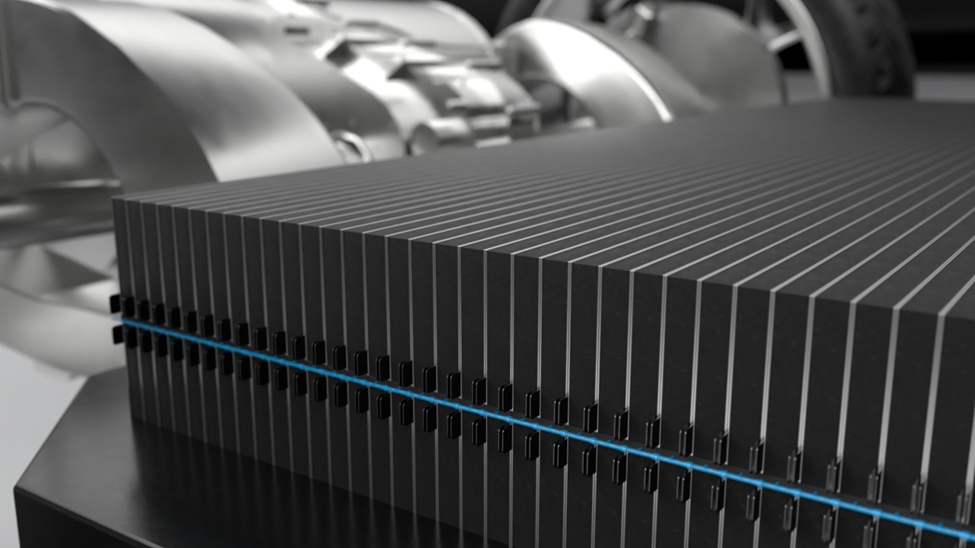
At the core of the I-BEAM XFC™ sits StoreDot's proprietary 100in5 cell technology, which enables charging 100 miles, or 160km of range in just 5 minutes. StoreDot’s 100in5 electrodes are assembled into its new I-BEAM XFC™ prismatic cells, which are designed to be incorporated directly into the battery pack.
Unlike traditional cooling systems, the I-BEAM XFC™’s patented Structural Cooling concept is embedded into the structure of each cell, providing enhanced thermal management. This prevents localized hot spots and maintains uniform temperatures across the battery pack, enabling it to accept the ultra-high currents required for fast charging, with minimal system overhead.
Conclusion
As OEMs seek to expand their model lineups to satisfy the demands of an ever-increasing and diverging range of consumers, the role of the battery cell’s form factor in giving manufacturers the design flexibility to meet unique strategies is likely to intensify.
Currently, there is no unanimous winner in terms of battery cell format, with the industry embracing all three configurations to cater to different needs and strategies. The battle is not only about energy storage but also the physical design that influences critical aspects such as thermal management and overall efficiency – with each cell form factor offering unique solutions.
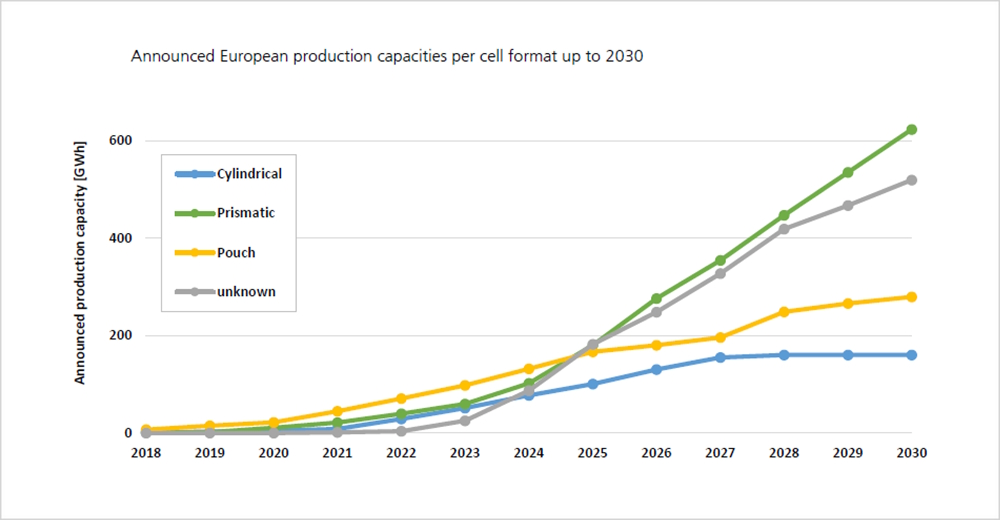
However, the consumer’s demand for extended range, fast charging EVs with long life cycles is likely to trend towards larger format, fast charging prismatic cells – possibly in the CTP format – or even incorporated as a stressed member into the vehicle’s chassis.