Extreme fast charging (XFC) is a key enabler to mainstream adoption of electric vehicles. Recharging an electric vehicle in minutes replicates the drivers’ convenience of fueling a tank.
However, current lithium-ion batteries are unable to support charging the electric vehicle in minutes without adverse consequences of capacity fading and serious safety concerns. Forcing such high-power charging as XFC in a traditional graphite-based chemistry adds significant stress to the battery and endangers the entire car.
By their nature, lithium-ion batteries have non-linear behavior so that fast charging of an empty battery – up to around 60 percent of their maximum available capacity, defined as state-of-charge (SOC), is considered reasonable.
To that end, various smart charging algorithms have been developed that are based on battery's SOC, in particular they take advantage of fast charging when the battery is relatively empty, and then the algorithm tapers off the charging current when the SOC reaches about 50 to 60 percent.
However, stress on the battery structure typically builds up in the second half of the battery charge cycle towards a full charge when the acceptance of lithium ions in the anode active material becomes labored. Furthermore, fast charging, even when at low SOC (10%-50%), would inevitably lead to faster battery degradation. Such type of solutions allows for partial, infrequent, fast charging of the vehicle, but doesn’t deliver the driver’s experience that is needed.
To achieve a safe consecutive XFC solution - a new chemistry strategy is needed in order to overcome the undue stress. In such technology the following safety challenges have to be addressed, specifically when charging a battery in XFC mode:
- Formation of dendrites, metallic lithium, over time
- Unused energy that turns into gassing, metal plating and heat
- Swelling and shrinking of various active materials
- Charging fast in low temperature environment
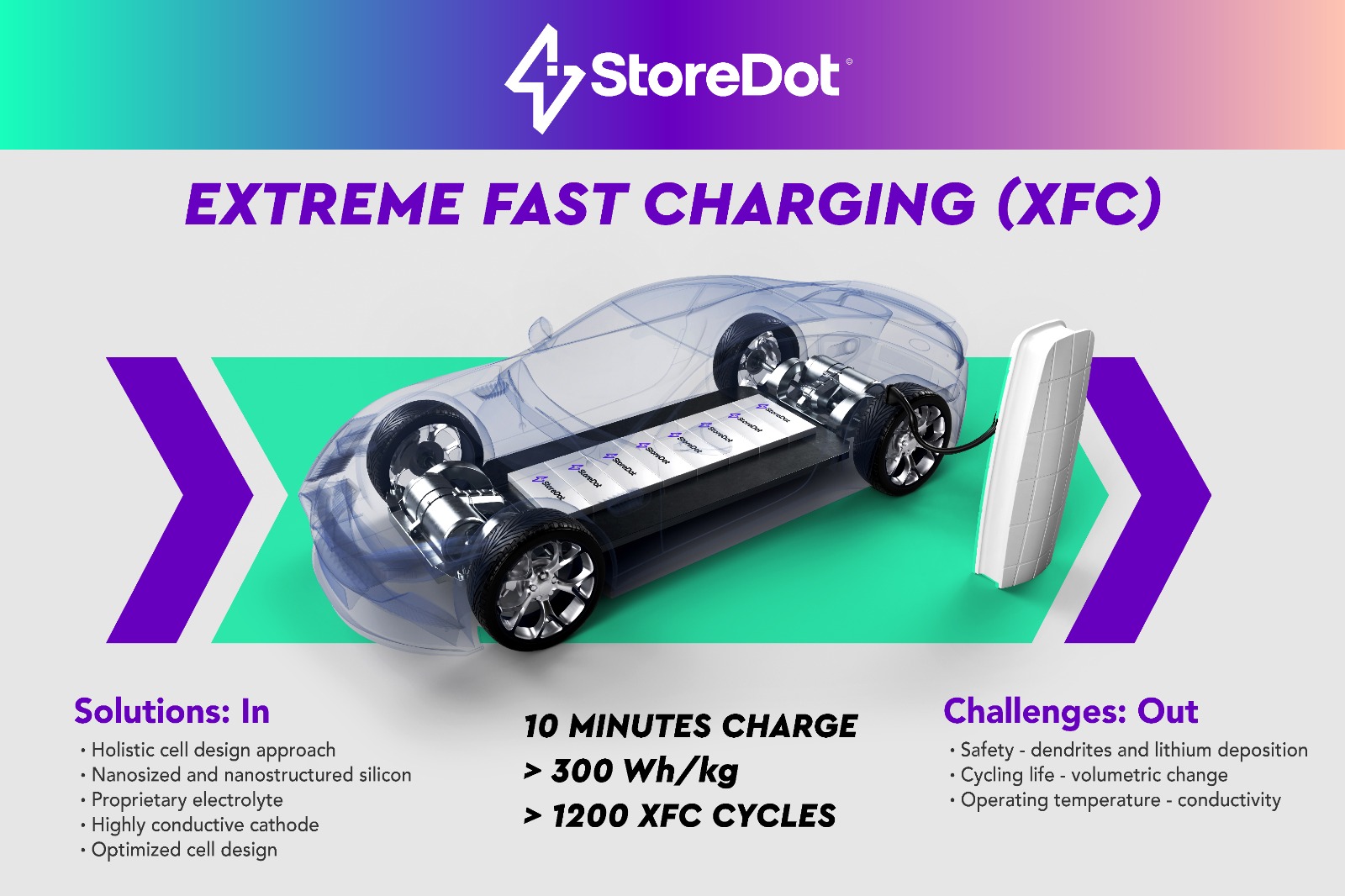
Technology breakthrough
Lithium-ion batteries are known for their inherent trade-offs among their key parameters. It is typically impossible to improve one performance property without sacrificing another. For instance, the electrolyte, which carries positively charged lithium ions from the anode to the cathode and vice versa through the separator, demonstrates good low temperature stability is often unstable at high temperature. Similarly, it is challenging to develop active materials that hold the lithium ions that are capable of high charging rates while maintaining their durability and safety over a wide temperature range.
StoreDot’s XFC technology reduces such inherent trade-offs by redesigning the science of the key battery components including the electrodes and the electrolyte chemistry. Therefore, a holistic view of the materials and the system electrochemistry of the battery cell is critical. StoreDot’s innovation integrates chemistry and engineering sciences, while applying a layer of artificial intelligence and machine learning to optimize overall fast charging performance. The resulting technology is being implemented in three types of cells - cylinder, prismatic, and pouch - all in various sizes and capacities, depending of the vehicle’s battery pack configuration.
Safety, Dendrites and Lithium deposition
The maximum charge current a lithium-ion battery can accept is governed by the cell design, and the active materials that hold the lithium ions. The goal of StoreDot's XFC technology is to avoid the known problem of metallic lithium plating which damages the battery and is also a safety concern.
Battery charging and discharging rates are generally limited by the resistance due to ionic diffusion within the active particles. For high power and fast charging, nanometric scale particles are introduced in order to compensate for the inherently slow ionic diffusion. A graphite-based anode with a high porosity and nanometric scale of its particles might be capable of fast charging due to the larger surface area and lower resistance. The energy density of such cell, however, is limited. In addition, the lithium deposition process occurs if the charge rate exceeds the ability of the anode to incorporate sufficient lithium. Therefore, fast charging in a graphite-based battery may cause metallic plating, and dendrites that can puncture the separator and cause fire and even an explosion.
Volumetric change and Cycling life
Silicon can be a good replacement for graphite as it holds more energy and better ionic diffusion. However, silicon is a challenging anode material to work with because it expands volumetrically up to 400 percent upon full lithium insertion. During battery operation, electrodes with high percentage of silicon undergo significant expansion and contraction, causing huge stress on the anode. As a result, anodes that use 100 percent of silicon are not practical, and thus only three to eight percent of silicon is typically added to graphite-based batteries.

Conductivity and Operating temperature
None of today’s electric vehicles can withstand charging in minutes. This is particularly true in cold, or even cool, temperatures due to the above-mentioned risk of lithium plating.
As such, fast charging technology must be region- and weather-independent to be truly competitive with internal combustion engine cars. Any battery's internal resistance is greatly influenced by the ionic conductivity of the electrolyte and the connectivity pathways within the electrodes. It is therefore essential to increase the ionic conductivity of the electrolyte as well as improve the contact area between the electrolyte and the electrodes in order to allow for XFC.
StoreDot solution
With such key design factors in mind, StoreDot’s battery reduces charging times from hours to minutes. Through the holistic design and by replacing the conventional graphite anode with silicon-based nanoparticles, XFC can be achieved.
StoreDot’s anode production process is based on dispersing nanosized silicon particle in a unique conductive organic and inorganic matrix to accommodate the silicon volumetric changes and maintain overall mechanical integrity. In addition, unique electrolyte, including several organic additives synthesized in-house, stabilizes the cell system over many charge and discharge cycles. Those additives play a crucial role in the electrolyte, and provide critical advantages including better safety, thermal stability and long cycle life.
Combining these elements of silicon-based anode in conjugation with highly conductive cathode, improved thermal efficiency, optimized ratio between electrodes, and customized electrolyte enable high energy density while delivering extremely high rate of lithium insertion. This mechanism demonstrates sufficiently low probability of risk of lithium dendrites and better overall safety of XFC.
StoreDot's battery testing has shown more than 1,200 consecutive XFC cycles before reaching 80 percent of the rated capacity. With energy density of over 300Wh/kg, this silicon dominant battery is among the most energy dense currently on the market, and the only one capable of true XFC.
Innovations in battery chemistry and materials, such as the XFC from StoreDot can offer the needed charging experience for drivers, and ensure that the accelerated adoption of electric vehicles worldwide.