As the world of mobility transitions from vehicles powered by internal combustion engines to electric vehicles (EVs), the demand for Li-ion batteries is expected to grow exponentially. With all-electric vehicle sales expected to grow to approximately 50 million in 2030 - accounting for about 50 percent of the new vehicle market – the demand for Li-ion EV batteries could grow to about 4,300 GWh.
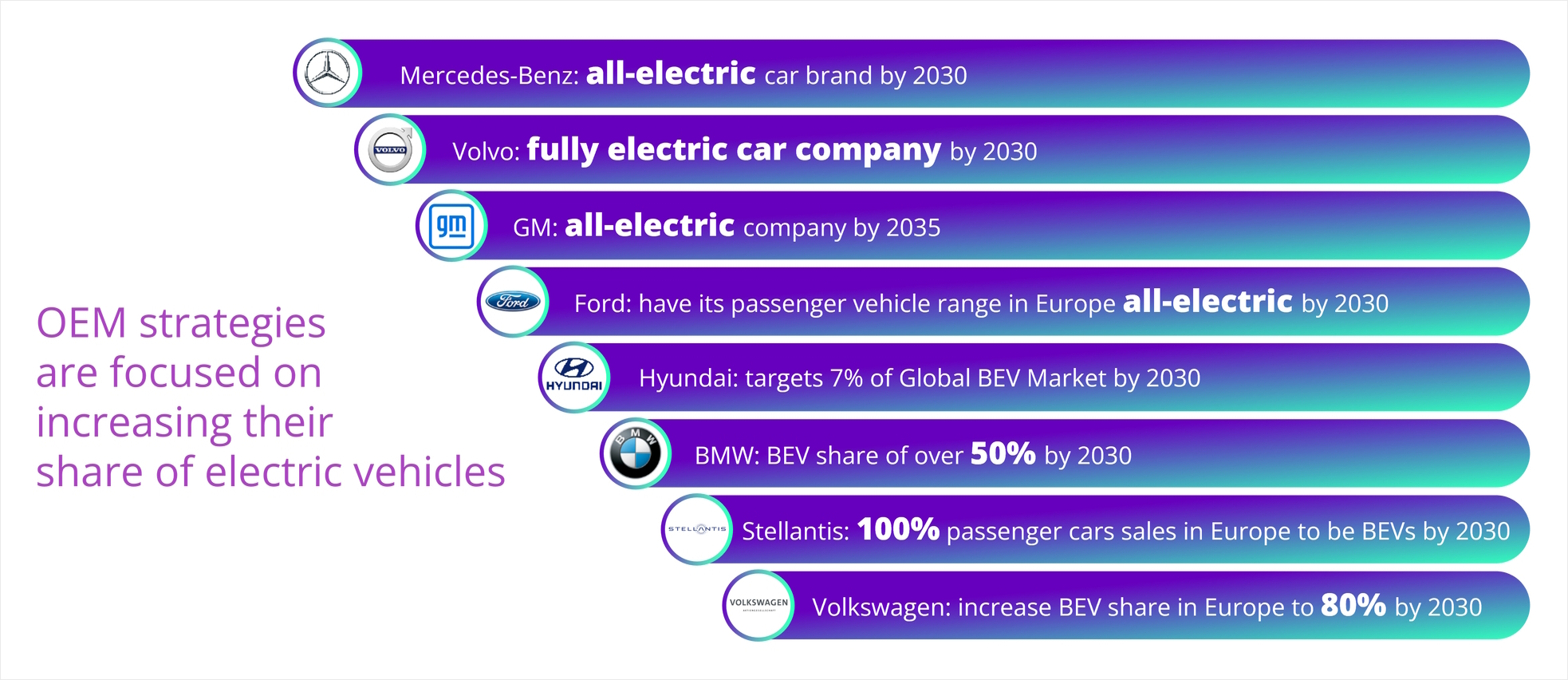
To support this growth, an additional 120 to 150 new battery factories will need to be built between now and 2030 globally. These will come in the form of ‘Gigafactories,’ capable of producing up to 90 GWh per facility.
However, as more consumers opt for owning a battery electric vehicle, battery cell manufacturers are increasingly coming under pressure to satisfy demand. Not only must the industry rapidly scale capacity, but also, with new technologies constantly emerging, researchers, production and process engineers have to develop and streamline the equipment and processes to continue to be very cost-efficient benefitting from high manufacturing yields and economies of scale without escalating CapEx.

And with EV OEMs taking full advantage of nascent battery technologies to meet consumer demands for safety, range and fast charging, battery cell manufacturers are looking for ways to utilize the current billions of dollars existing depreciated production lines, with proven processes to contain costs and optimize the time to market.
The challenge: a battery cell shortage is anticipated by 2028
Li-ion battery cell production is not only complex but also costly. For instance, a planned $1.3 billion project in Arizona is expected to cost $127 million per GWh of production output.
Even with announced investments in new gigafactories totaling around $300 billion over the past four years, the demand for cells is still expected to outpace supply in the near future. Driven by demand for EVs and grid energy storage, a cell shortage is anticipated by 2028.
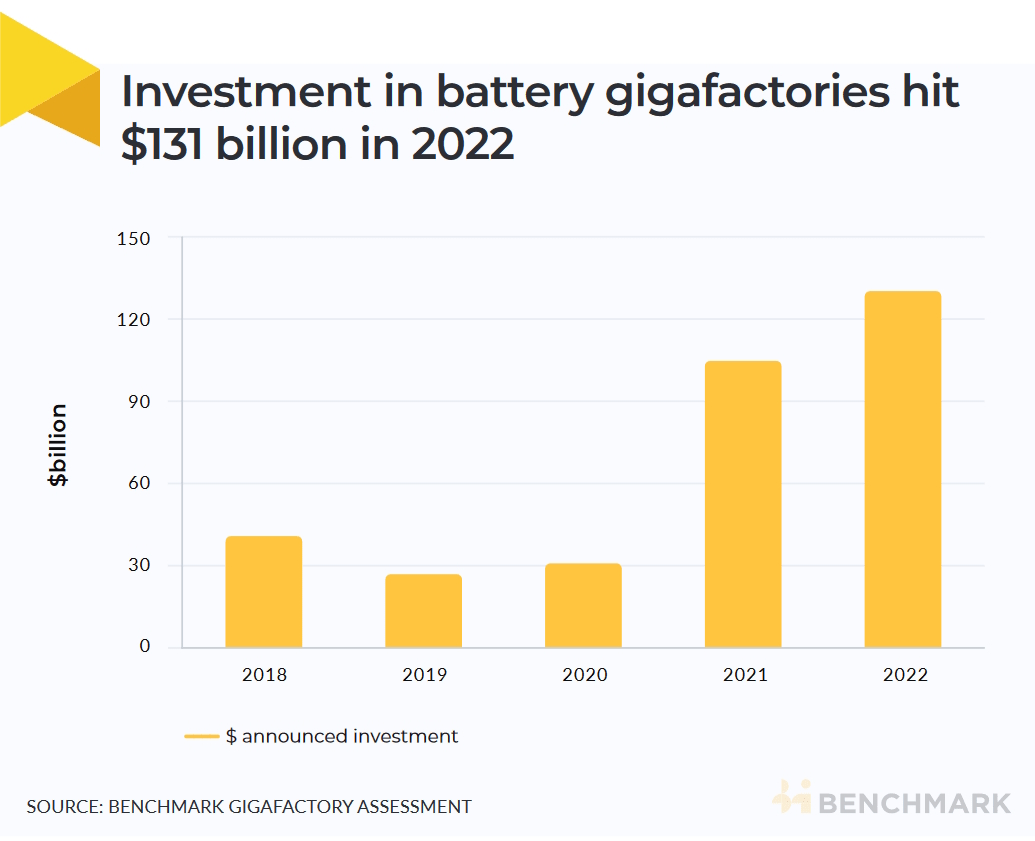
However, with the cost of increasing capacity in an existing plant being far lower and requiring less time to implement, the deficit could be reduced significantly. For example, to increase the capacity of an existing factory from 35 GWh to 50 GWh would require an investment of only $275 million.
And it is not only the CapEx manufacturers are concerned about – setting up a new production line and conducting the required trials to verify the process and product can be very costly and time consuming. Unexpected delays, that are not uncommon, further escalate the cost and extend the time to market.
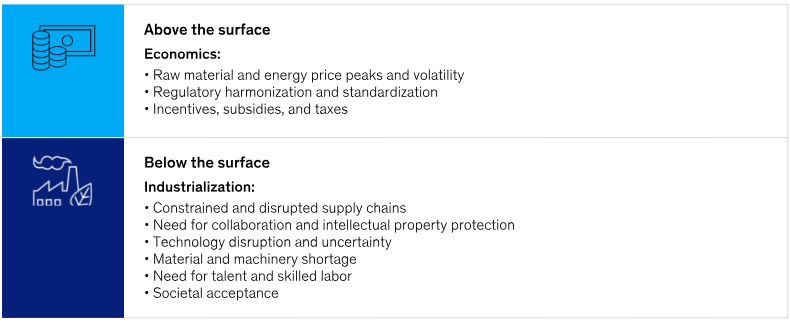
What is more, the race to innovate in any industry can initially lead to lower levels of quality. On new production lines applying untried processes, undetected defects during battery manufacturing can also lead to costly recalls for the EV industry.
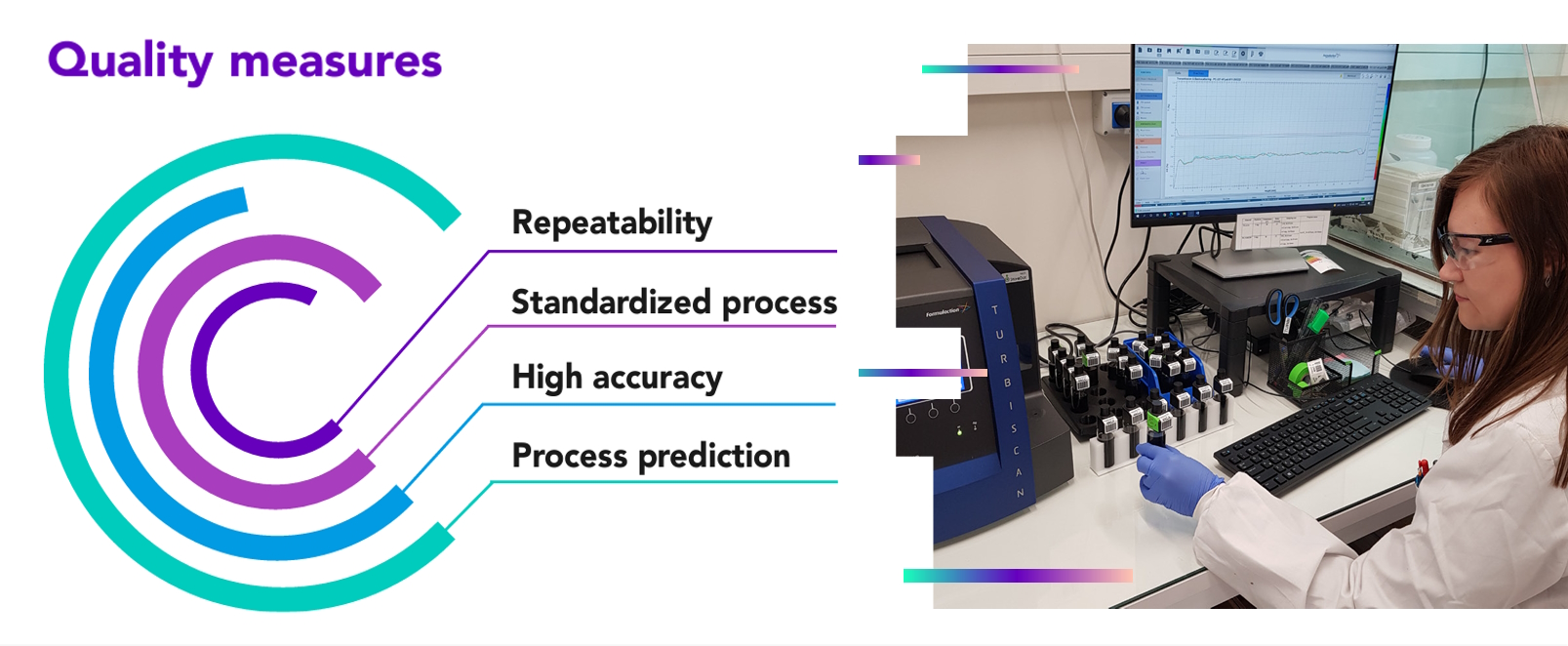
Many of these pitfalls can be eliminated with the utilization of existing production lines and processes.
Minimizing time-to-market: implementing new battery technology in months
Battery technology is always evolving. Developing battery chemistries that offer higher energy density, faster charging, longer lifespans, and improved safety is an ongoing challenge. Staying up-to-date with the latest advancements and integrating them into production processes is, at times, even more perplexing.
Thus, StoreDot’s “design to process” approach, allows its new and innovative technology to be easily implemented on a battery manufacturer's standard Li-ion production line.
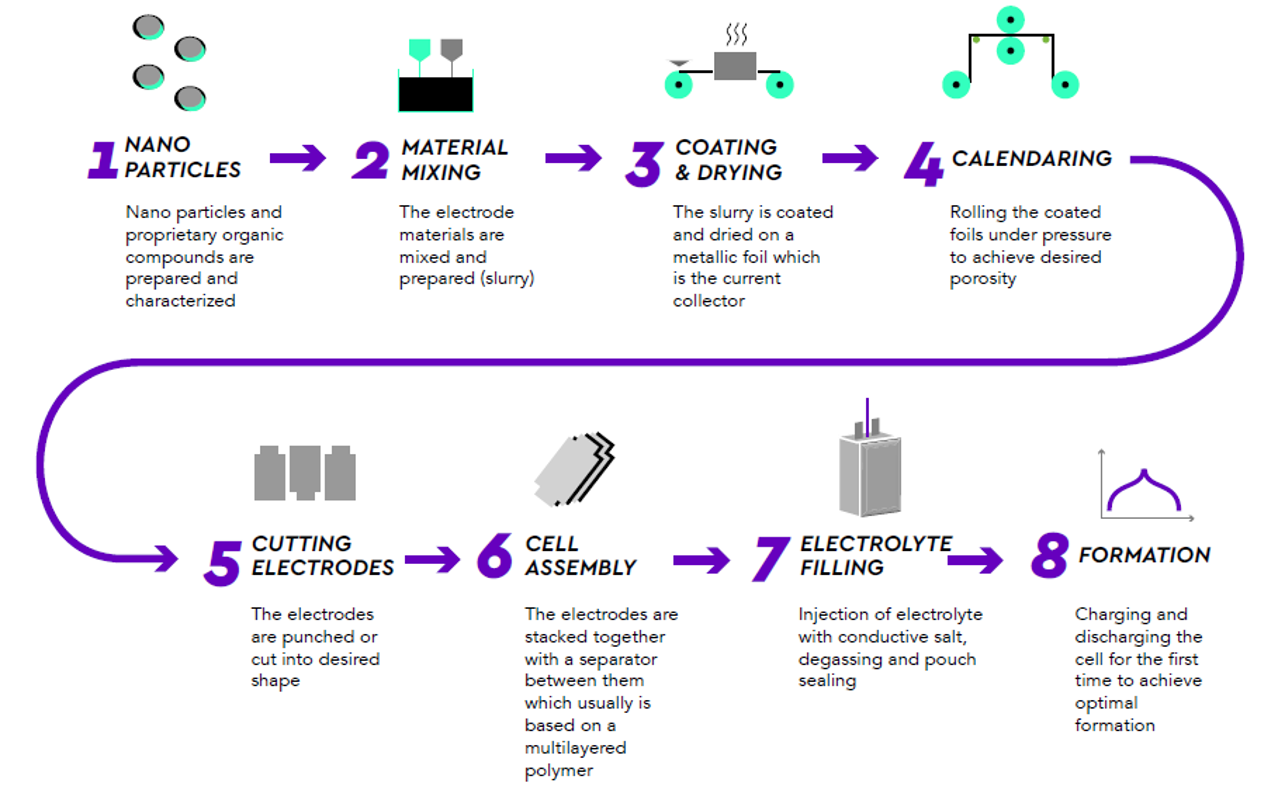
This significantly shortens the time from the end of development to production of batteries by all accepted standards, and therefore offers OEMs significantly shorter time-to-market, as well as lower CapEx associated with constructing new production lines to increase manufacturing capacity.
In the case of StoreDot's 100in5 technology, its design-to-process approach enables the rapid scaling of production of its extreme fast charging (XFC) battery cell on existing Li-ion manufacturing facilities. This allows battery producers to integrate extreme fast charging technology in a variety of the common battery form factors, without a drastic redesign of the production line. In practical terms, StoreDot’s manufacturing partners were able to implement the technology on standard Li-ion production lines and start producing EV-grade battery cells within months. This proactive process design philosophy offers EV OEMs the opportunity to speedily introduce cutting-edge technology that eases consumers’ range and charge anxiety, into their product lineup and consequently- into their upcoming EV models without the risk associated with the introduction of new technologies that require special equipment or new process.
Conclusion: closing the gap
To meet the global market of 100 million cars, with an EV share of 50 percent, battery manufacturers are going to be hard pressed to build enough new factories to meet the 4,300 GWh these vehicles will require. Faced with the need to reduce costs, the investment of USD1.22B in an average 20 GWh gigafactory also requires careful consideration, as does the time to market for batteries built on entirely new production lines.
To achieve the scalability the growth in EV sales demands, StoreDot has optimized a comprehensive development cycle, from the chemistry formulation through testing and scaling up to production. StoreDot’s XFC technology can be easily mass produced on existing production lines with standard processes, as the development of the cell is industrially oriented, simple, scalable, and fully compatible with existing lithium-ion battery technologies.
Being able to implement advanced battery chemistries on existing production lines greatly contributes to closing the gap between the growing demand for EVs, and the lagging race to build more and more giga factories to support the demand. While the utilization of existing production equipment and processes simplifies production, cuts costs and speeds up the time to market, its real impact is in reducing the cost of EVs and giving manufacturers the ability to speed up the introduction of high-performance technologies that satisfy consumers’ demands. The result is the acceleration of the uptake of battery electric vehicles.