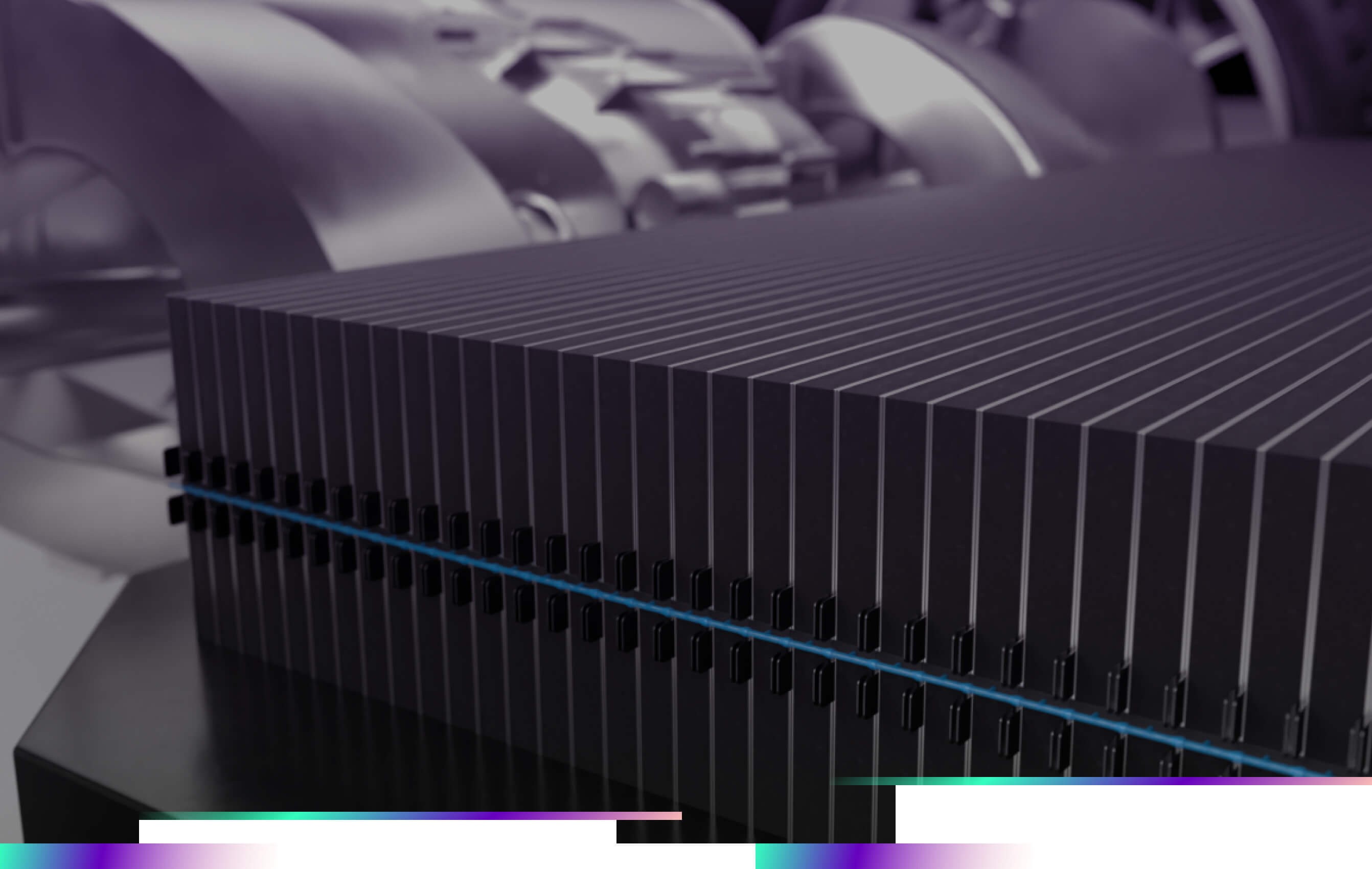
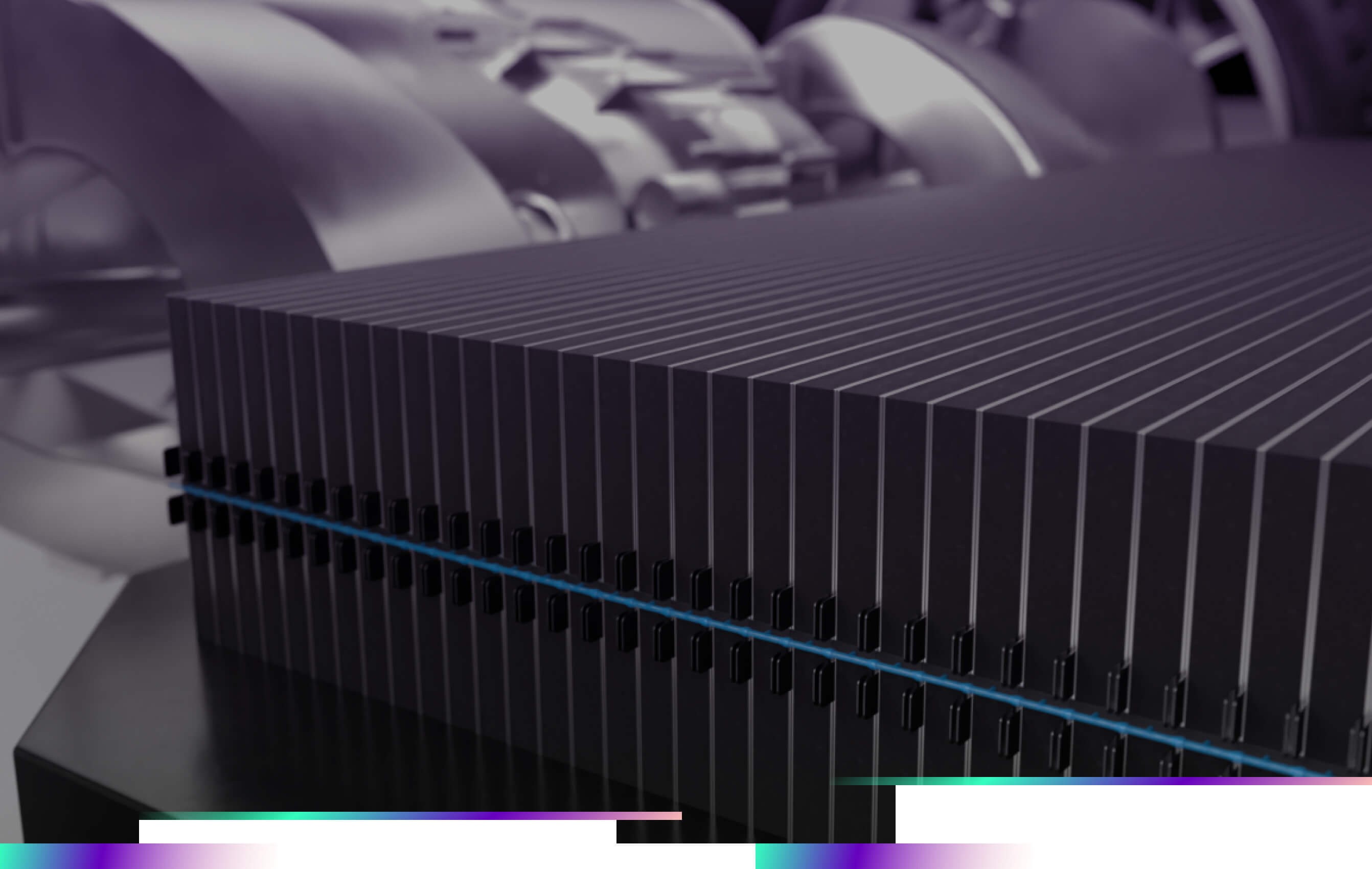
EXTREME FAST CHARGING: FROM CELL TO PACK
ELIMINATING
CHARGIng ANXIETY
To become more competitive and meet the demand of consumers,
EVs need to have longer ranges and shorter charging times.
Most available models today fall short of this proposition; the current standard for fast charging of EVs is around 30-45 minutes for an 80% charge.
StoreDot’s current technology supports a charge of 100 miles (or 160 km) per 5 minute of charging, and is working on improved technology that will allow to reduce the charging time for 100 miles, or 160 km, to 3 minutes, within few years.
EXTREME FAST
Charging Trends
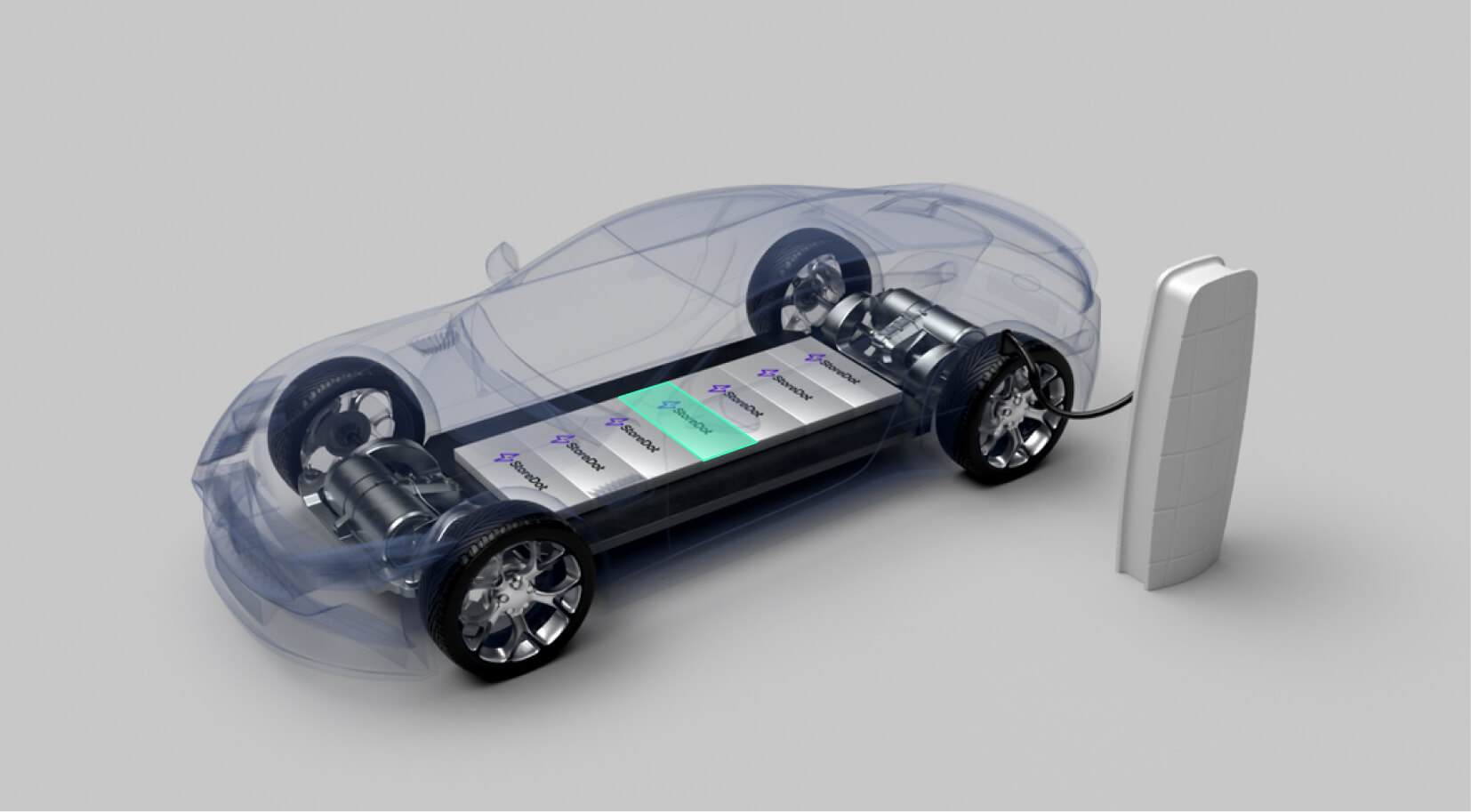
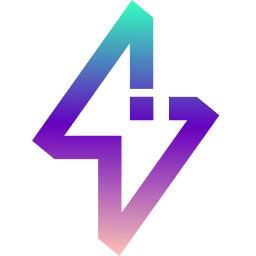
- An improved battery chemistry is essential in order to provide 25-30%
higher volumetric energy density, longer range and even faster charging times. - Improved, flexible packaging configuration

- High power charging infrastructure needs to be expanded and upgraded to allow for faster charging and to offer greater accessibility to the growing number of EV owners seeking a fast charging capability.
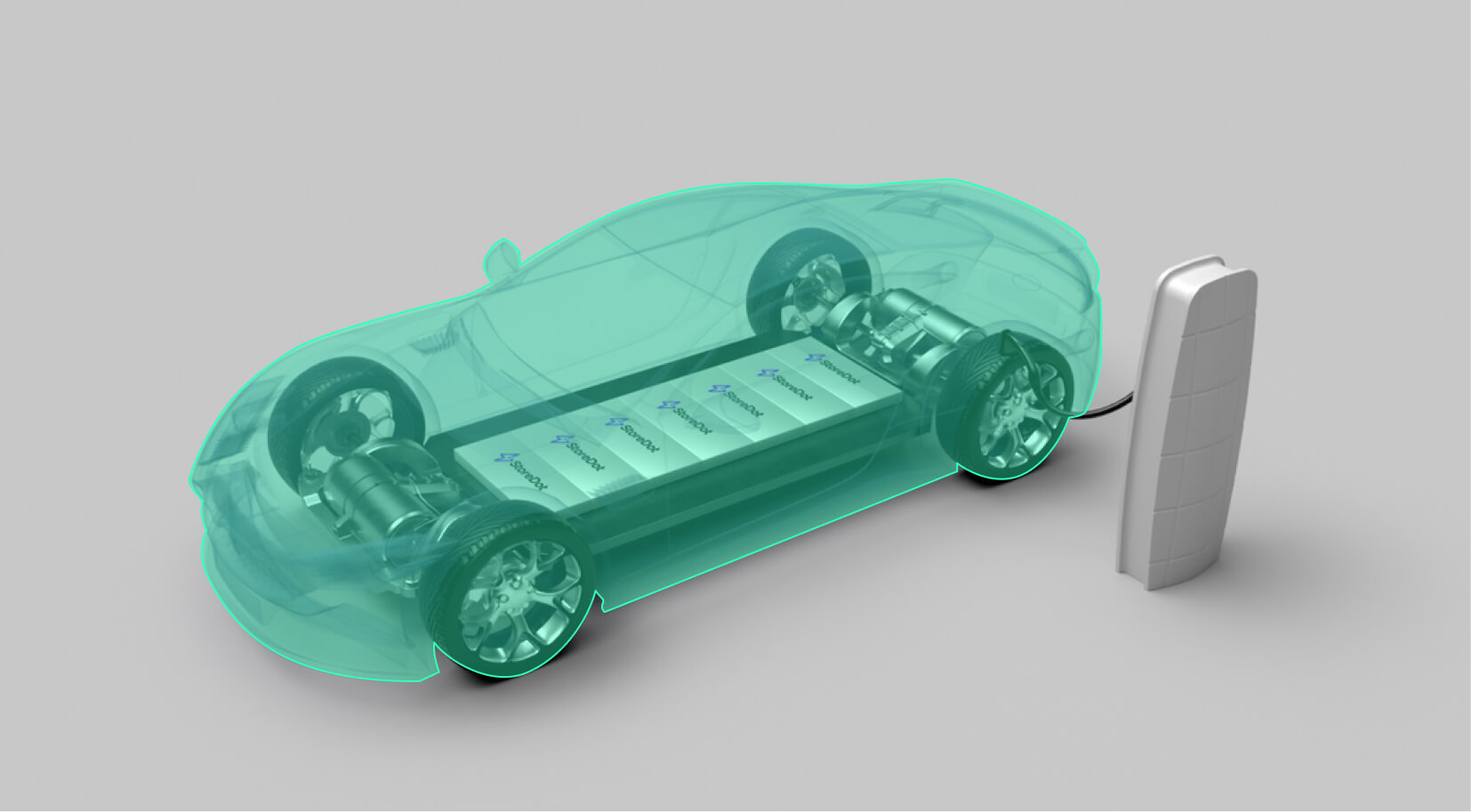
- The overall weight of the vehicle should be optimized to increase the energy efficiency of the power train.
- A lighter battery pack is closely related to the weight, efficiency and maximal range of the vehicle.
EXTREME FAST CHARGING
SILICON BATTERY
storedot’s 100inX
solution roadmap
100in
940 Wh/l**
(340 Wh/kg**)
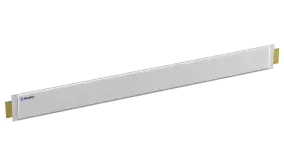
(320 Wh/kg)
~550*110*9 mm
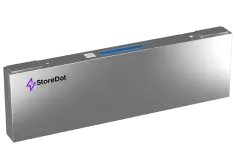
(295 Wh/kg)
~300*90*25 mm
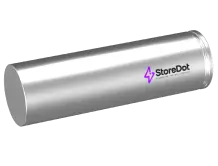
(285 Wh/kg)
4695
100in
1020 Wh/l**
(370 Wh/kg**)
100in
1070 Wh/l**
(400 Wh/kg)
for 2032
100in
500Wh/kg
*100inX = 100 miles (160km) charged in X minutes; chemistry is compatible with all cell form factors
**Energy density figures represent net value - J/R electrodes, separator and electrolyte only
Battery Packaging
Flexibility
Having the right chemistry alone is not sufficient.
The battery has to be adaptable to the vision and configuration each car maker is pursuing.
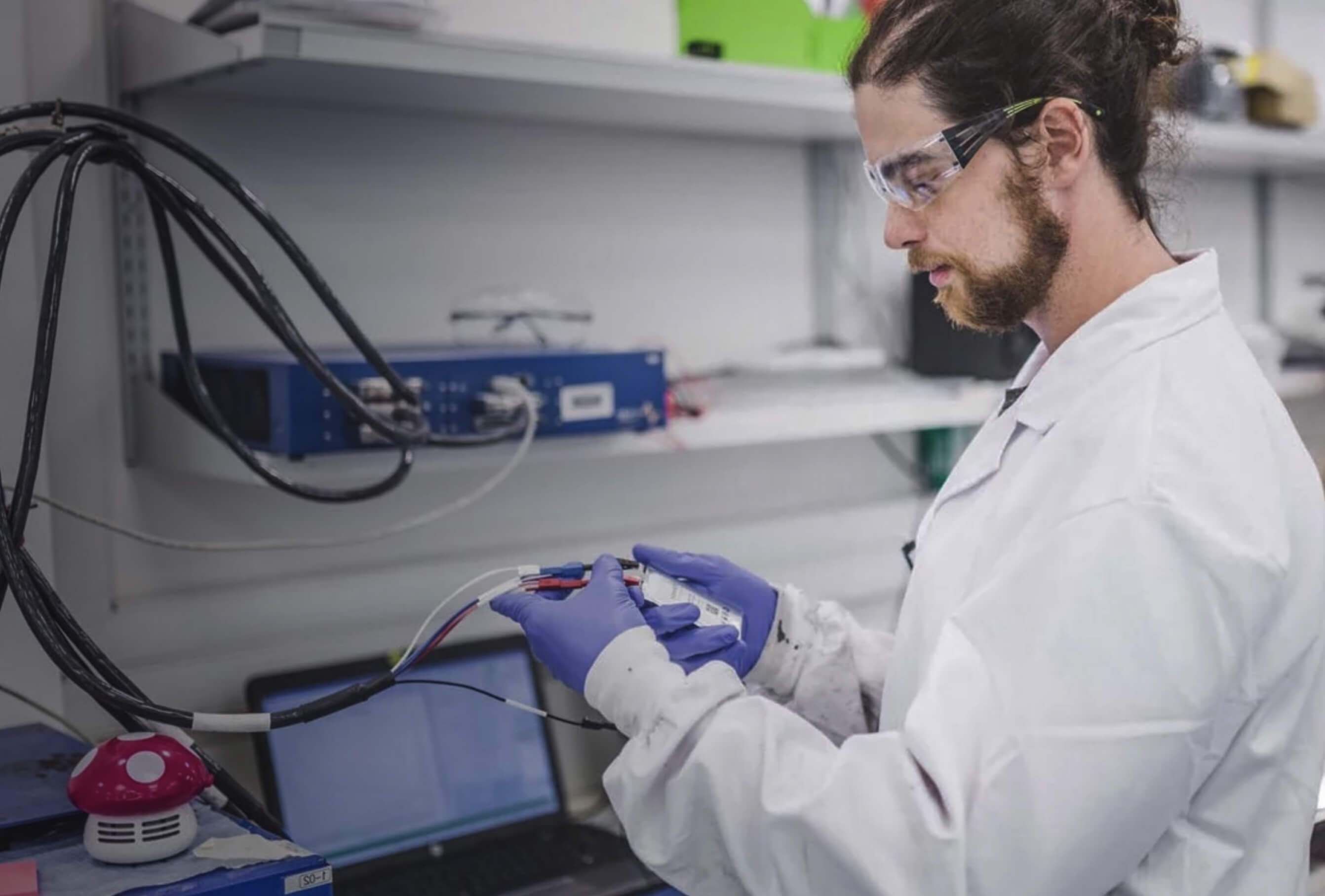
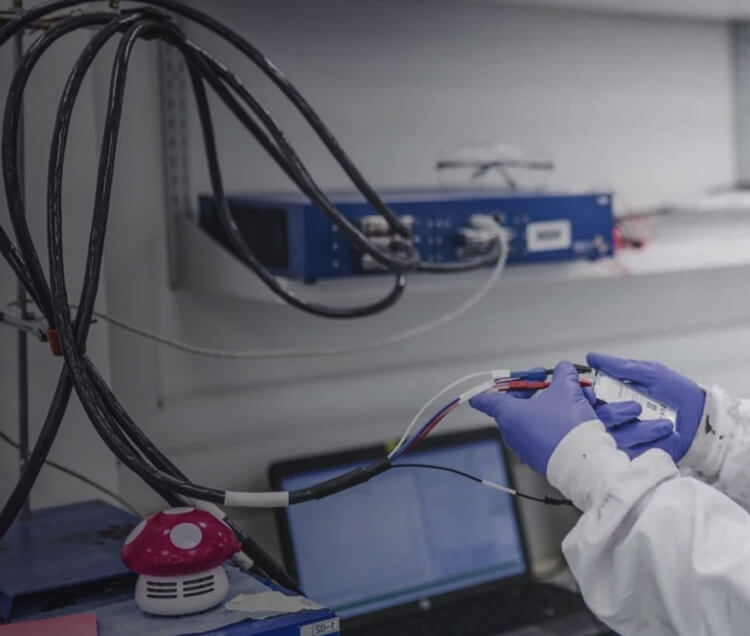
MANUFACTURING READINESS
Optimizing pack-level
energy density
I-BEAM XFCTM: Shifting from cell-level chemistry to a holistic pack design
Cell-to-pack involves directly connecting individual battery cells to form a larger battery pack; cell-to-chassis involves mounting the cells onto a structural chassis, which also serves as a heat sink dissipating heat generated by the cells during operation, and a support structure for the cells.
The benefit of using these approaches is that they provide the necessary support and protection for the battery cells. In a cell-to-pack system, the cells are tightly packed together and secured within a protective casing, which reduces the risk of damage from vibration, impact, or thermal expansion. StoreDot’s I-BEAM XFCTM cell-to-pack configuration also simplifies the manufacturing process, minimizes part count and reduces the weight and volume of the battery pack.
white paper
Learn how StoreDot's innovative Cell-to-Pack Concept overcomes traditional EV system integration challenges while enhancing range and safety.
Enhancing
vehicle systems
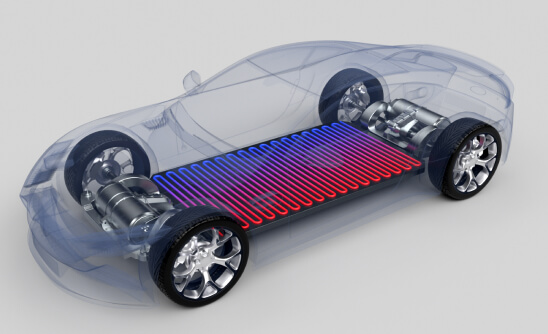
EV battery cooling is a crucial aspect of ensuring the efficient and safe operation of an EV. The battery cooling system is designed to regulate the temperature of the battery pack, especially during high-power usage, to prevent overheating and ensure optimal performance. The cooling system works by circulating a coolant through the battery pack to remove heat generated during charge and discharge cycles, then recirculating it through the battery pack. The design of the cooling system depends on various factors such as the type of battery chemistry, the size of the battery pack, and the operating conditions. Through optimization of the cooling system, the battery pack can operate efficiently and safely, helping to increase the range and reliability of the vehicle.
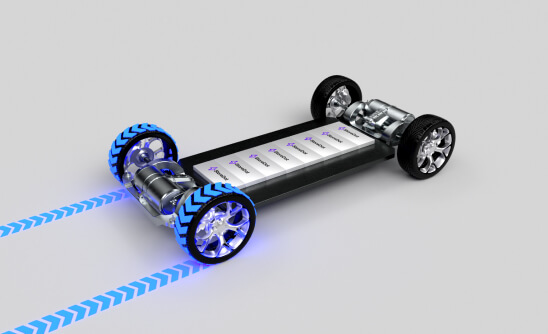
the Kinetic Energy Recovery Systems (KERS) designed for the electric powertrain requires no additional hardware – the existing traction motor that powers the vehicle acts as a generator when braking or coasting, with the energy thus harvested stored
in the lithium-ion battery (LiB). This is referred to as regenerative braking,
or simply “regen.”
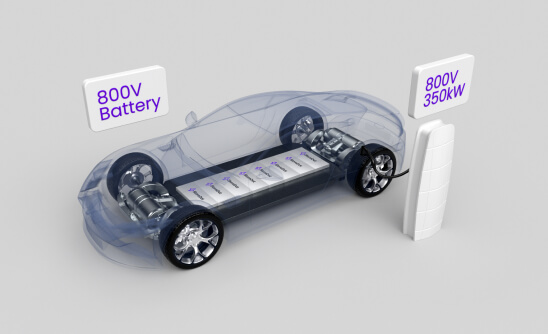
EV's battery pack voltage is based on the multiplication of the total cells that are in series configuration at the pack and their nominal voltage. Fast-charging an EV by a fast-charger is usually limited by the heating degree of both the EV's powertrain and the charger electrical components, which is squared-correlative to the charging current. By increasing the vehicle's pack voltage, the overall current through the systems could be decreased, leading to higher charging-power and higher charging-rate, while generating the same heat. The nowadays path to higher voltage packs will befit to the fast-charging segment.
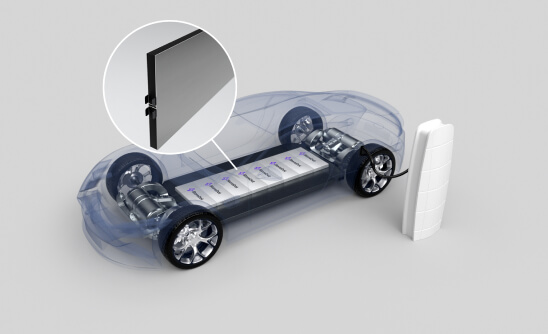
The battery pack is one of the most critical components of an electric vehicle (and plays a major role in determining its efficiency. In addition to storing energy, a structural pack functions as a physical support to the vehicle. By integrating structural battery packs into a vehicle's design, manufacturers can reduce weight and improve efficiency, safety and mechanical durability. Eliminating redundant components is particularly important in electric vehicles, where weight is an important factor in achieving range.
.webp)