Initially seen as a viable alternative to lead-acid storage devices, lithium iron phosphate batteries - commonly known as LFP (lithium ferrophosphate) – make use of low cost, readily available, LiFePO4 in the cathode. Because of their low cost, low toxicity, well-defined performance, and long-term stability and safety, these LFP cells rapidly gained a footing in the manufacture of electric vehicle (EV) batteries.
However as EVs grew in popularity, consumers, used to the functionality of fossil-fuelled transport that dominated the market for over 130-years, began expressing apprehension over certain aspects of the technology. Disturbingly consumer surveys were clearly telling manufacturers drivers were especially anxious about the limited range of many mainstream all-electric cars.
Thus, because of LFP’s relatively low nominal voltage and limited energy density, manufacturers began looking at alternative cathode chemistries to overcome consumers’ range anxiety.
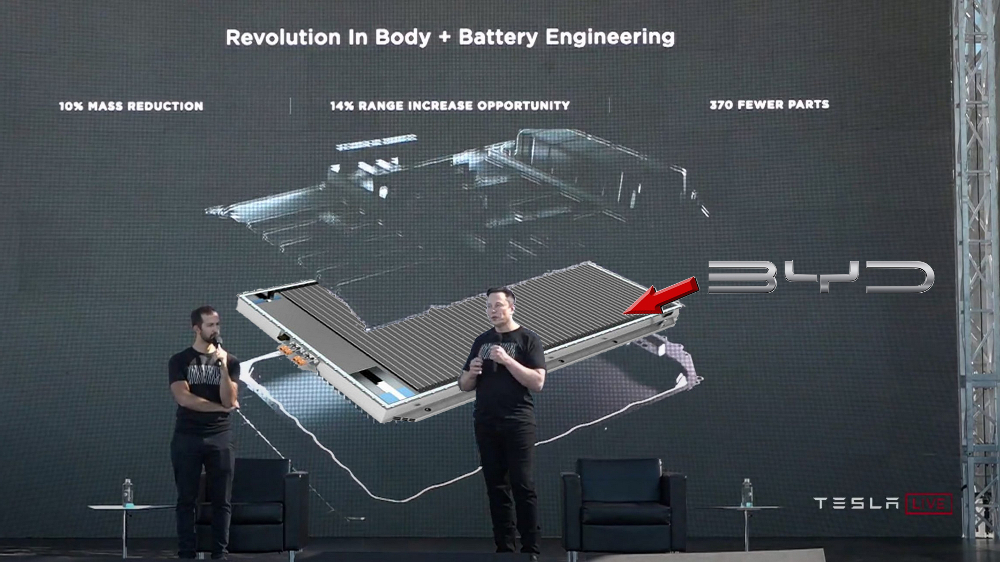
In so doing manufacturers have largely focused on increasing the battery’s energy density. Consequently, traction battery cathodes have seen a significant migration from LFP chemistry to ternary layered oxides - nickel–manganese–cobalt (NMC) and nickel–cobalt–aluminum (NCA).
This move pushed the global market share of ternary batteries to a record high of 90 percent in 2019, and it was widely believed that future EV batteries would converge on ternary cathodes increasingly rich in nickel. A higher nickel content still achieves an excellent specific capacity whilst reducing demand for expensive and strategically vulnerable and socially questionable cobalt.
However, even though LFP cathodes lose out to ternary chemistries’ energy density they offer cost and safety benefits without any of the strategic threats that accompany the scarce materials required in high energy cathodes.
So, presented with these compelling benefits of LFP batteries many manufacturers are reevaluating their approach to battery energy density as related to the EV.
The rationale behind the interest in cell-to-pack design
Inspired by a shared vision of a cost-effective, high-performance, and safe battery, the majority of EV manufacturers have gravitated to a common battery pack configuration consisting of numerous battery modules. Each of these modules is made up of groups of individual battery cells. These modules and cells are typically liquid-cooled, and intelligently monitored and managed by battery management systems.
However, this modular design is not ideal. For example, the inactive areas of the module - the housing, terminal plates, side plates, internal connectors, battery management, and cooling systems - add weight, take up precious volume, and ultimately compromise the pack’s energy density.
Given these shortcomings, many EV and battery manufacturers are eliminating modules entirely, choosing instead to implement cell-to-pack (CTP) designs that integrate (large format) cells directly into the battery pack.
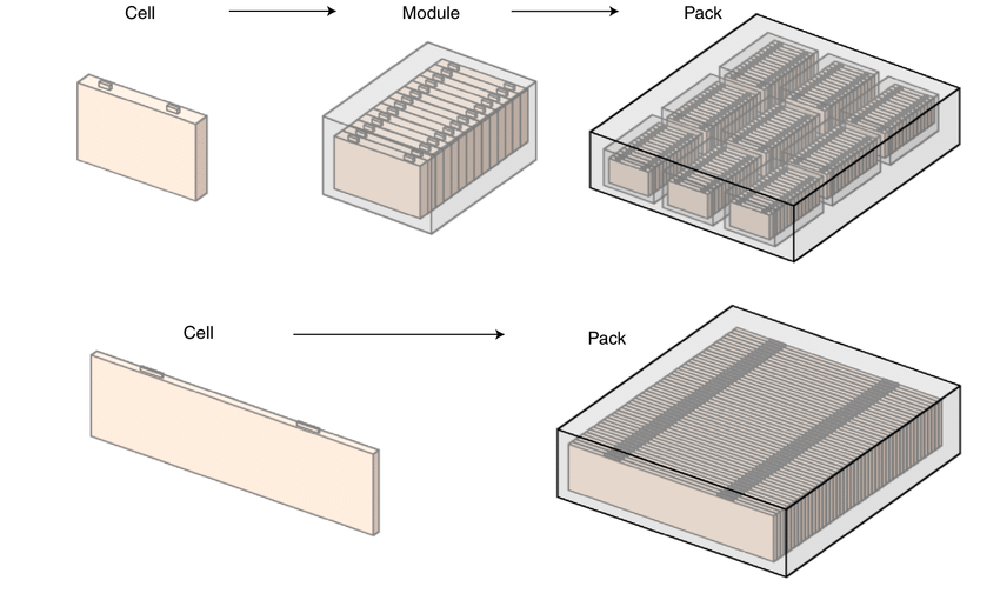
CTP holds the potential to increase volume utilization by about 15 to 50 percent, depending on the battery cell format. Moreover, the number of parts can be reduced by up to 40 percent. Following this design philosophy manufacturers can also opt to use the gains in pack energy density to use cheaper, less energy-dense cells, such as LFPs.
Thus, while it is true that the energy density of LFP chemistry lags that of NMC and NCA at a cell level - state-of-the-art LFP cells achieve specific energy of about 180 Wh/ kg, compared to NMC and NCA cells that have already achieved >250 Wh/ kg - applying CTP technologies significantly reduce the gap at the pack level.
Cell-to-pack designs that boost energy density
As the leading manufacturer of EVs, Tesla has gained a reputation for vehicle efficiency. This, largely due to its cylindrical format ternary batteries – whether 1865, 2170, or soon 4680.
However, producing the Model 3 in China for the Chinese home market presented Tesla with an opportunity to explore the benefits of equipping these vehicles with LFP batteries. And to minimize the impact on range Tesla opted to use prismatic cells in a CTP approach.
The decision to switch to LFP was a tactically important one for Tesla. Driven by the need to guarantee supply of the strategically vulnerable Nickel and Cobalt materials required for high-performance applications such as the roadster and Semi-truck, and Chinese consumers’ greater tolerance for shorter range, Tesla switched to LFP batteries in May 2020. Globally, all standard range Model 3 and Y’s will follow suit.
The efficacy of Tesla’s CTP approach can be measured by the vehicle’s performance. While the energy density of LFP cells is typically between 15 and 25 percent lower than the alternatives, the CTP batteries in the Shanghai-made Model 3 deliver a volumetric energy density of 359 Wh/liter. This translates into a range of 253 miles for the Tesla Model 3 SR with the LFP battery, compared to 263 miles for the nickel-cobalt-aluminum pack.
Building on the CTP design philosophy of increasing the energy density at a pack level through optimizing the active volume of the battery, BYD have come up with a ‘blade’ battery where single cells span the full width of the pack, offering a cell-to-pack integration efficiency improvement of over 50 percent. While the nominal Voltage remains at 3.2 Volts with a gravimetric energy density of 166 Wh/kg the CTP architecture increases the volumetric energy density to 448 Wh/liter.
Of course, the intrinsic safety of LFP when compared to ternary chemistries, such as NMC, makes it an ideal candidate for these large-format cells. For instance, the onset temperature for a self-sustained exothermic reaction for NMC811 is 232 °C with 904.8 J/ g of thermal energy released, compared to LFP’s wide but flat exothermic reaction peak of between 250 and 360 °C releasing only 147 J/ g of thermal energy.
This superior safety is confirmed by China’s National Big Data Alliance of New Energy Vehicles that released a report showing that 86 percent of EV safety incidents from May to July 2019 were related to EVs powered by ternary batteries with only 7 percent attributed to LFP batteries.
However, in large capacity cells typically used in CTP battery packs the charging/discharging characteristics of specific cells are bound to vary widely from one another, and even degrade at different rates. This imbalance not only impacts performance but can even pose a safety risk.
To ensure all cells in the pack perform at their peak StoreDot has patented a “self-healing” system that makes use of a suite of software algorithms with corresponding hardware to identify and proactively recondition a cell or string of cells back to an optimized performance level. This ensures homogeneous cell performance across the pack at all times.
And as interest in CTP technology grows, manufacturers are finding innovative ways to further optimize these battery packs. So, while active liquid-cooling has become the norm in EV design, the cooling systems require pumps, plumbing, and coolant, which sap energy and add weight.
Applying a novel approach to CTP design in which passive cooling (air cooling) is used to dissipate heat from the battery pack, Mercedes-Benz’s Vision EQXX concept car achieves a claimed range of 621 real-world miles from a battery pack of less than 100 kWh. This equates to more than 6 miles per kWh.
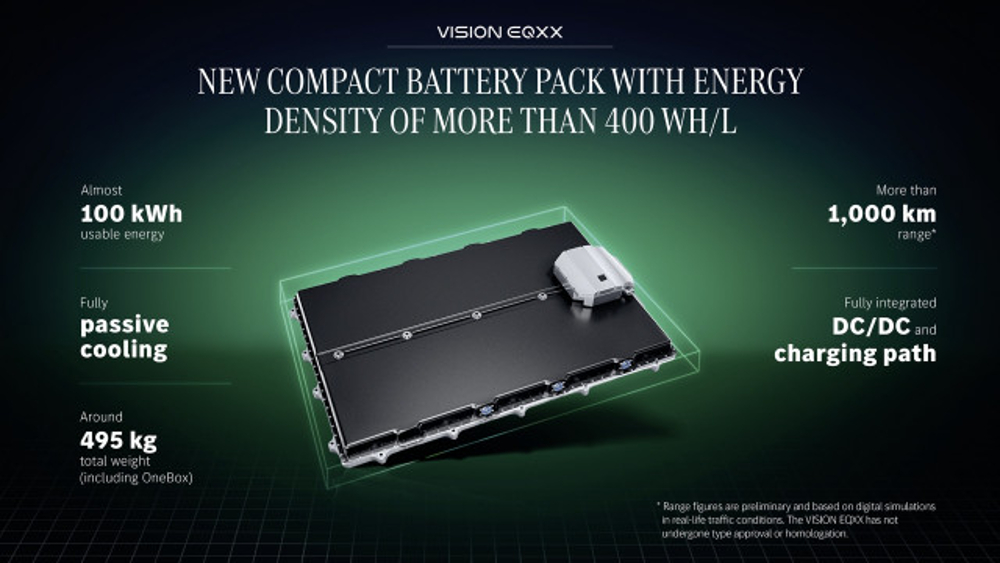
This passive cooling is accomplished with intelligent cell management throughout the pack, combined with an integrated cooling plate at the bottom, as well as vents that open as the temperature increases.
According to Adam Allsop from Mercedes-AMG’s High-Performance Powertrains, passive cooling allowed the design team to slim down the profile of the battery and fit a huge energy content into a very small space. Mercedes-Benz claims the pack to be 30 percent lighter and half the size of that in the EQS, with an energy density of nearly 400 Wh/liter at the pack level.
Thus, while the various cell-to-pack designs and technologies are not dedicated to resurrecting the LFP battery, given the energy density, safety, and cost of large-format LFP cells in CTP battery packs there is no doubt LFP will stage a comeback in many applications. Already in China LFPs make up 57 percent of the battery production for electric vehicles.