The broad consensus across the battery and automotive industry was that by 2025 battery electric vehicles (BEVs) would reach cost parity with their internal combustion engine (ICE) powered counterparts. This would follow as an inevitable consequence of falling battery prices.
However, it hasn’t quite worked out that way, with the hypothesis derailed, temporarily at least, by the recent increases in energy and material costs. This has led to many pundits revising their forecasts, with the industry doubling up on efforts to make BEVs more affordable.
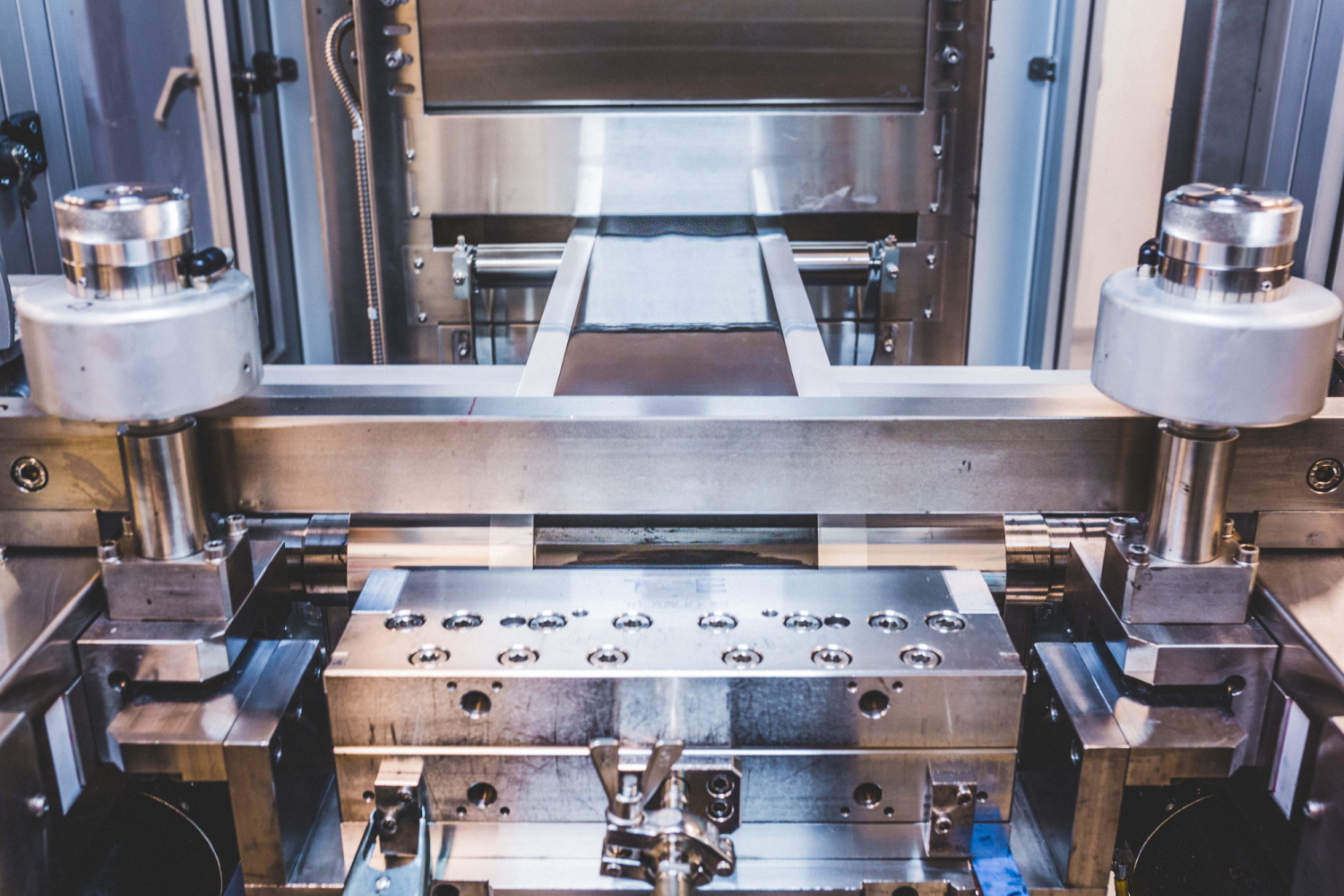
With EV economies of scale still relatively low, many studies have confirmed that EVs in the small- to midsize-car segment and the small-utility-vehicle segment often cost $12,000 more to produce than comparable vehicles powered by internal-combustion engines (ICEs).
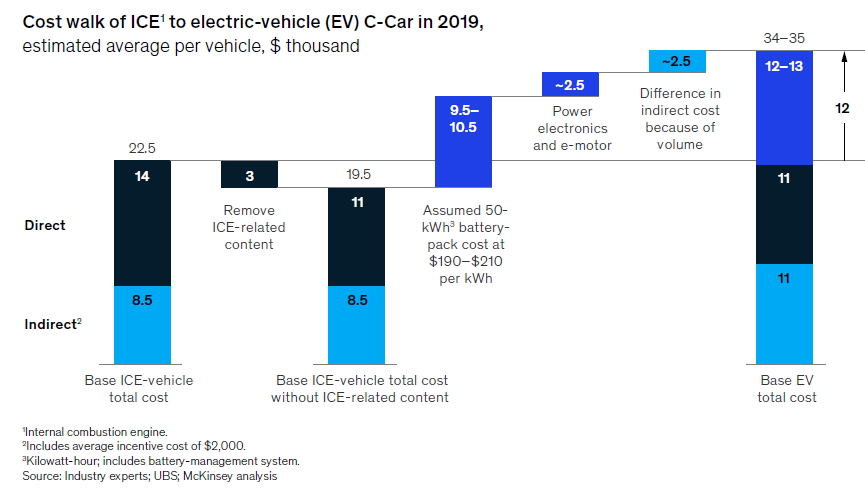
This disparity is largely due to high battery costs that typically make up between 35 and 50 percent of the total price of an EV. Battery costs still represent the largest single factor driving EV affordability, even though the US Department of Energy asserts that lithium-ion battery (LIB) pack prices dropped by 87 percent between 2008 and 2020.
In addition, LIB raw material prices have recently spiked upwards, threatening to put the brakes on battery-pack price reductions. Following the war in Ukraine, prices of nickel and aluminum have been breaking records. Lithium and other important raw materials are also becoming more, with lithium having more than doubled since the end of 2021.
This unprecedented surge in raw material prices, combined with the increasing cost of energy, currently impacting many battery manufacturers, will almost certainly put EV battery price declines on hold until 2024, with average battery prices increasing by 5 percent in 2022.
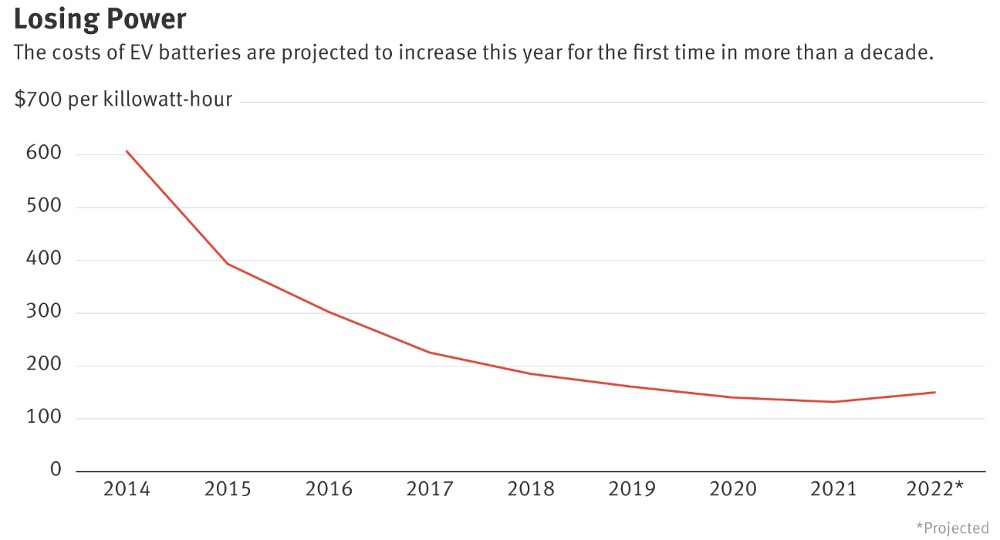
Even so, with increased adoption of batteries, alongside improvements in manufacturing and battery technologies, the long-term trend is likely to still be towards lower battery costs and increased affordability, as economies of scale and cost-reduction engineering take hold.
Scalability boosts economies of scale
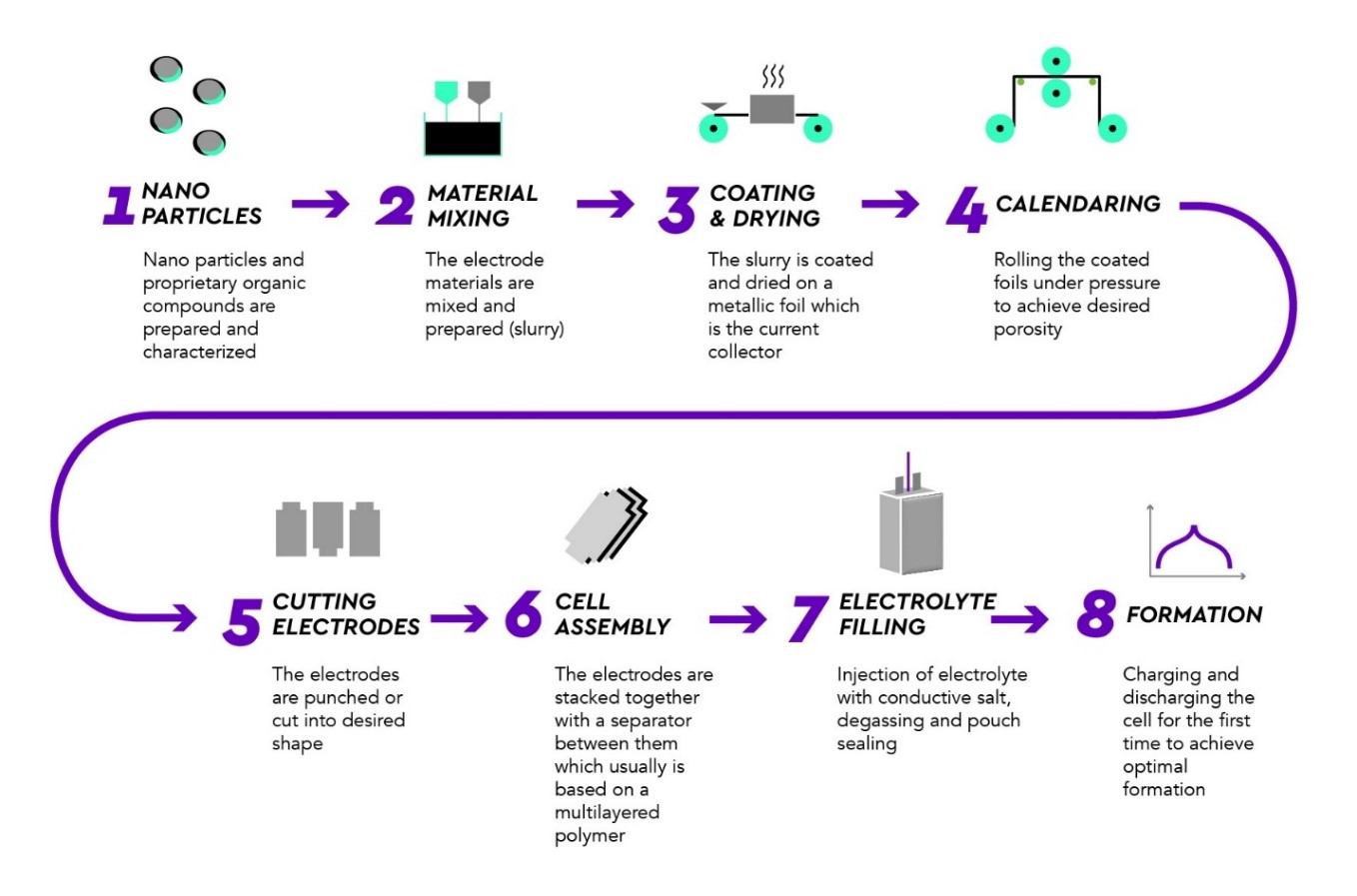
With the market for battery cells growing, on average, by more than 20 percent per year until 2030, it is likely to reach $360 billion. There is also a realistic scenario in which the market accelerates and hits $410 billion by 2030. That could happen if the industry follows the path of other renewable technologies such as solar and wind and enters a virtuous cycle in which increased scale drives down costs. If this occurs, it will almost certainly stimulate EV sales.
However, to realize these economies of scale, the manufacture of battery cells has to be scalable. Cell manufacturing, the most important step in the battery value chain, is estimated to account for up to 40 percent of battery-industry value creation by 2030. It is therefore important, when considering the design of the cell and choice of chemistry, that these fit standard supply chains and manufacturing processes.
With more than 300 battery gigafactories currently under construction or planned around the world, Dr. Richard Kim, an analyst at IHS Markit, believes establishing scale in battery manufacturing will play a critical role in the period through 2025. At least 5 GWh to 10 GWh of capacity per region will be a minimum scale for production.
This inevitably brings us to the question of pioneering technologies, such as all-solid state battery cells, that require unique production lines, equipment, and manufacturing processes. Are they able to scale at a pace that achieves competitive pricing against cells already being built at scale in existing facilities?
Even the expected performance gains of these nascent technologies may not be enough to offset the potential cost premium over chemistries such as that deployed by StoreDot in its silicon-dominant LIBs. These cells achieve good performance at lower costs by virtue of their relatively uncomplicated manufacturing process and the fact that they can be produced at scale on standard Li-ion production lines.
Sheer production scale is critical to driving battery cost down and making EVs more affordable. But production speed and yield rate serve as an equally important cost reduction lever. Thus, chemistries that require less-complex processes are likely to be better suited to higher-speed, higher-yield manufacturing.
Reducing costs through selective cell chemistry, materials, and battery pack design
Until recently, the industry consensus was that boosting range was the top priority. This has led to a proliferation of battery cell chemistries with cathodes containing ternary layered oxides such as nickel–manganese–cobalt (NMC) and nickel–cobalt–aluminum (NCA).
However, many of these critical battery materials are mined in limited volumes, and due to supply constraints and steadily increasing demand have recently seen significant price increases. According to a recent report from S&P Global Commodity Insights, over the past year, the price of cobalt has ticked up around 85 percent, with nickel climbing about 55 percent.
To counter escalating material prices companies such as Tesla, Ford and Rivian are rethinking the trade-off between range and price, through the use of more abundant, lower-cost materials – in particular lithium iron phosphate (LFP) and its derivatives in the cathode. Although LFP batteries do not offer the same energy density, and consequently range, as cells with ternary layered oxide cathodes, the material cost is significantly lower. The more established production technology also leads to a lower manufacturing cost per kWh for LFP batteries with the price of LFP cathode active material (CAM) in China 43 percent less expensive per kWh, than NMC811.
And to retrieve some of the energy density lost at a cell level when using LFP, manufacturers are applying ‘cell to pack’ (CTP) designs, using large format battery cells that do away with the traditional modules. The cell-to-pack redesign optimizes space and weight and further cuts costs by simplifying cooling and battery management complexity and reducing the number of electrical connections.
Today, natural or synthetic graphite particles are used as the main constituent for the anode. However, as with many other LIB materials, prices of high-grade graphite used in lithium-ion batteries have risen from $530 per ton to $825 per ton from September 2021 to June 2022, according to Benchmark. The group expects that number to top $1,000 per ton in 2025 and to remain at “a high level” through 2030.
Fortuitously, in an effort to meet consumer demands for better performance manufacturers are adding small quantities of silicon to the anode with this expected to reach 10 to 20 percent by 2025.
Silicon-dominant anodes: not all are created equal
Whilst silicon may offset increasing graphite material costs, additional processing expenses need to be factored in. Thus the cost of the precursors, capital equipment, and manufacturing costs have to be weighed up.
For instance, adding silicon nanowires to commercial graphite comes to about $1.6 per kWh added to the energy storage capacity of the graphite. Since EV-grade graphite typically costs about $6 per kWh, the cost of the resulting composite anode active materials is lower, with the cost savings increasing as the number of silicon nanowires fused onto the graphite increases.
In addition, recycling will be able to return a substantial amount of the LIB material back into the supply chain, and circular economy applied to LIBs holds promise to reduce costs without detracting from performance.
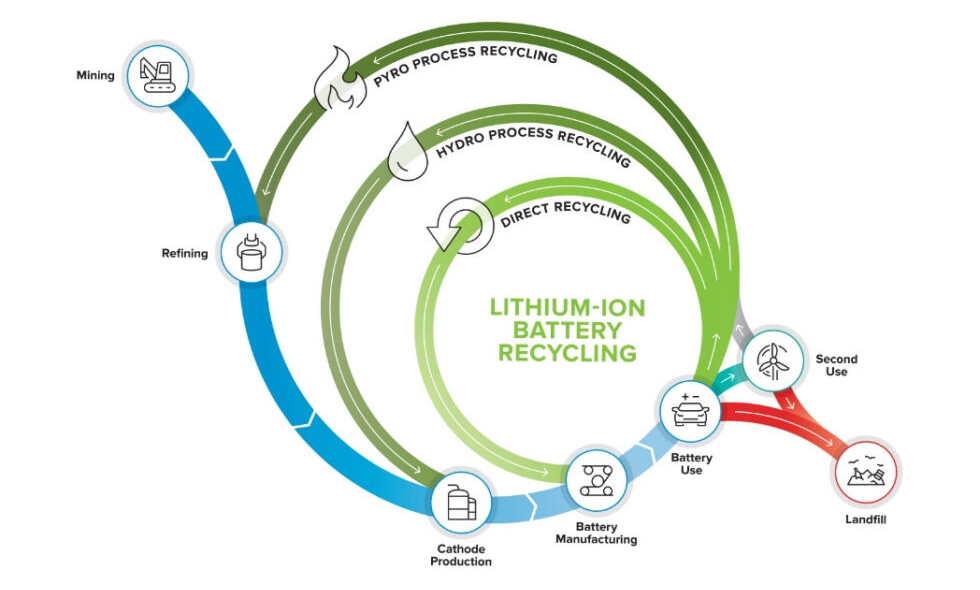
More than 4 million tons of LIB material available for recycling by 2030. And over the next 20 years, the amount of lithium-ion battery material that is recycled will grow from roughly 5 to 75 percent of all the material available.
With a cost of $32/kWh, this recycled material offers the potential to provide significant savings by offsetting mined nickel, lithium, and cobalt prices.
Summary
Rising LIB raw material prices certainly have the potential to delay the timeline on cost parity between EV and ICE vehicles, which could hamper the wider adoption of EVs.
Of course, when debating EV batteries, cost alone will never be the sole deciding factor driving the consumer’s purchasing decision. Nevertheless, there is a gradual realization within the industry that, to date, the issue may not have received the attention it deserves. After all, an EV battery that delivers a range of 500 miles and charges 100 miles in two minutes, but costs $200 per kWh is almost entirely academic for the buyer with a $25,000 budget.
Whilst luxury EV makers selling products for more than $50,000 are well supported, other than in the Chinese home-market the mainstream consumer with less than $25,000 to spend cannot afford the current offerings without tax breaks and incentives. EVs will only become sustainable when the technology and, above all the cost, meet expectations.
And in order to further drive down costs and speed up adoption it is important that the manufacture of the battery cells is cost-effectively scalable to ensure economies of scale are achieved in as short a time as possible. For this reason, StoreDot’s silicon-dominant Extreme Fast Charging battery technology has been developed to allow for the use of existing LIB production lines and processes.
Thus, whilst nascent exotic technologies, such as all-solid-state batteries may hold promise, a holistic range of factors must be weighed in when looking at the fastest time to market to enable mass adoption of EVs. A battery cell technology should be evaluated in context of scalability, including cost, manufacturability (does it require special equipment), and maturity – since achieving success in the lab is still very far from scaling up to high-yielding mass production.
This article was first published in Batteryline