Since the pandemic, supply chains around the globe have been disrupted. But it’s not just semiconductors that are hard to come by, so too are employees with the right skill sets.
If your company has a need of qualified people in IT and Data, Sales and Marketing, Operations and Logistics, Manufacturing and Production as well as Customer Facing and Front Office, you’ll be only too aware of this, as these five sectors are currently the most in demand.
So severe is the global skills shortage, that it is the worst it has been since 2006. According to a recent survey published by workforce solutions provider ManpowerGroup, 75 percent of employers questioned reported difficulty filling roles.
But there’s an even more worrying skill shortage in a sector that, if not rapidly resolved, may prevent the future our planet so desperately needs from arriving, or at least seriously delay it. I am referring, of course, to the global battery industry and consequently the much-needed global adoption of electric cars.
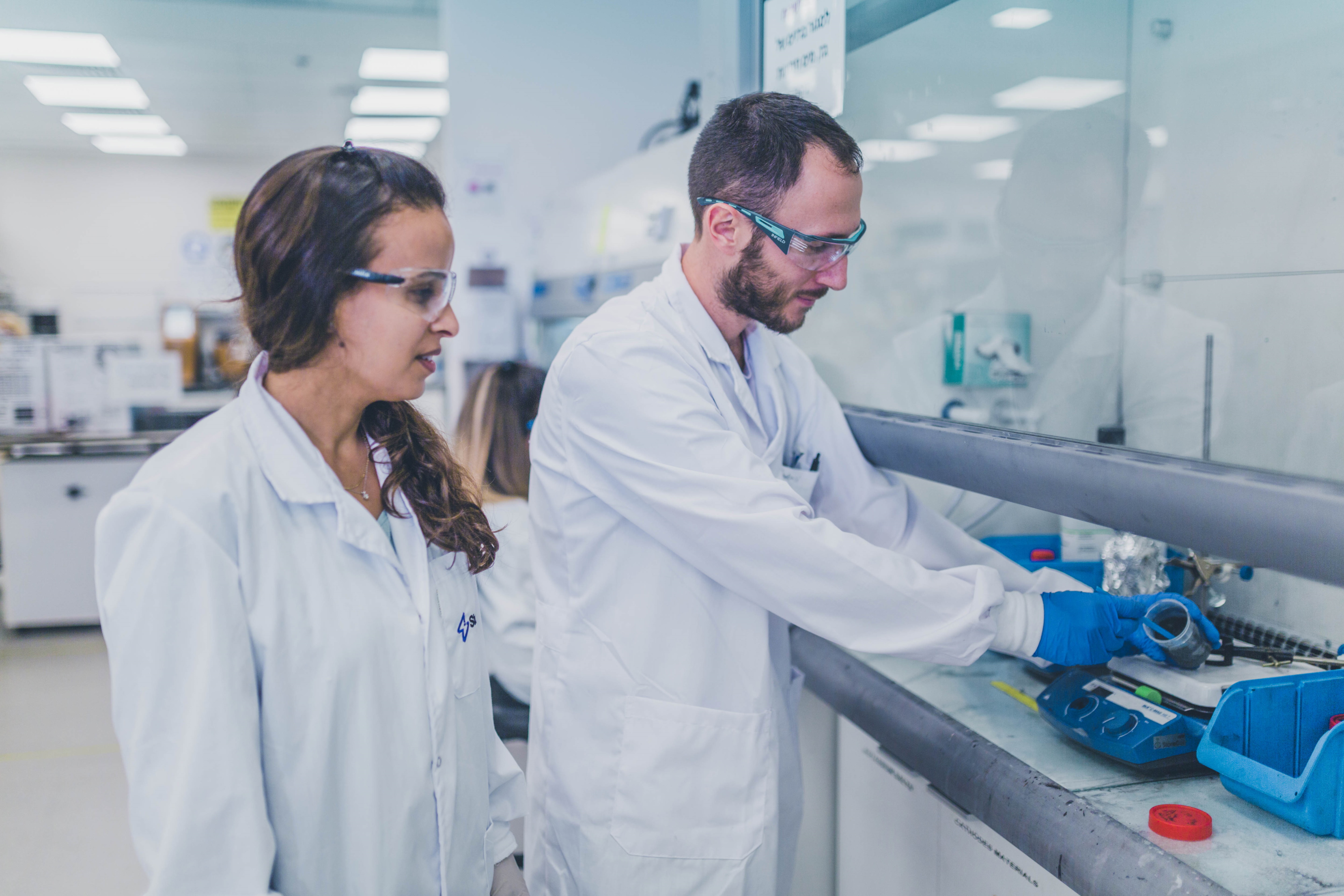
The battery sector is currently grappling with a huge dearth of skilled people. The shortage is most acutely felt with advanced battery experts, electrochemists, material scientists, and professionals with experience in bringing battery solutions to market at the required quality and scale. The industry is also desperately short of experts in pack design, cooling, safety, and battery management systems. The situation can be summarized as a lack of skilled researchers and technical workforce with sufficient knowledge of battery commercialization.
The issue affects every stage of the supply chain. Right at the source of the industry, we need to learn how to mine the raw materials required more effectively and sustainably. To do that, we need to develop new chemistries, but the industry just does not have enough people with the skill set to do so as the need grows in the immediate future.
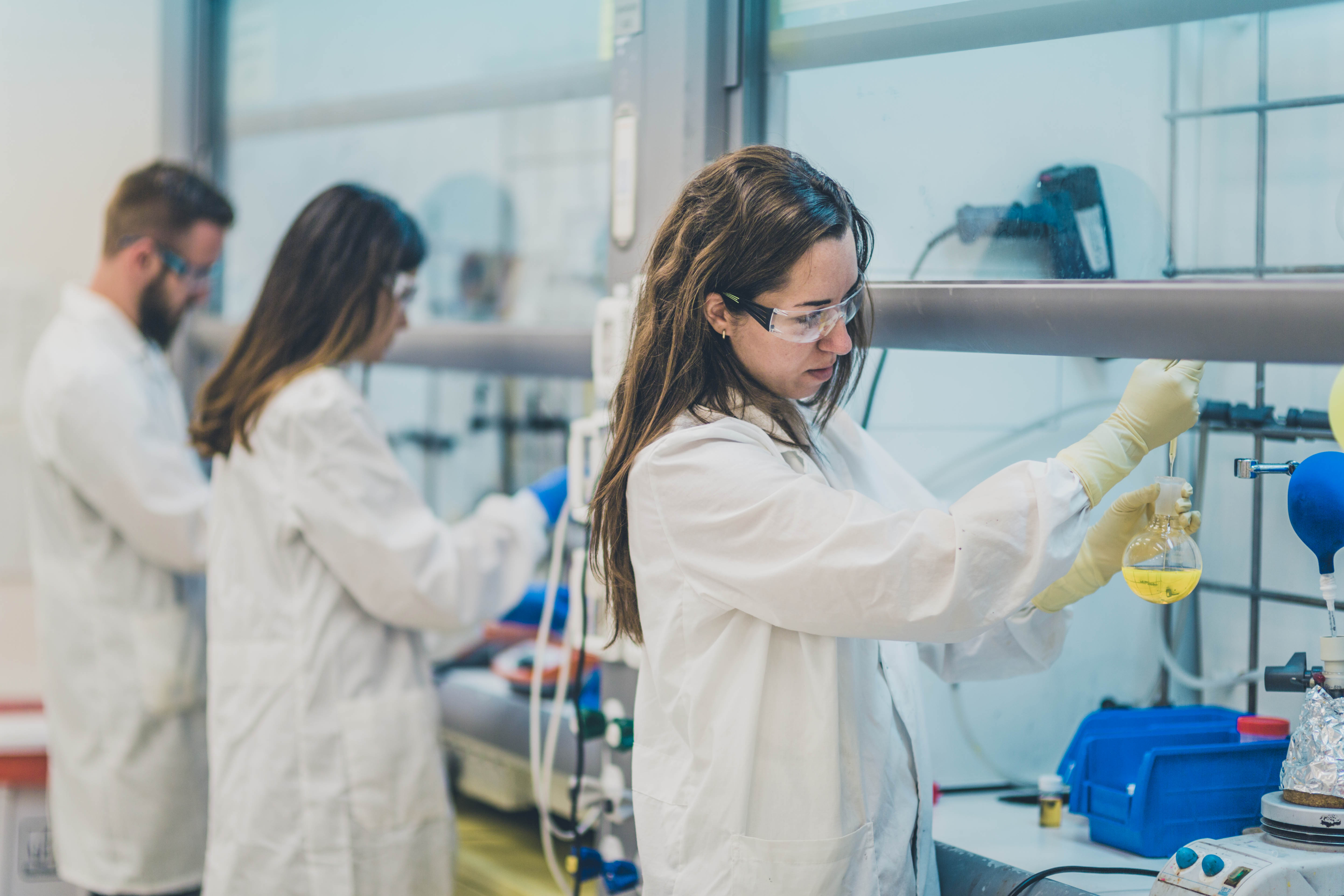
Global challenge
The European Battery Alliance planning group estimates the EU's battery industry needs 800,000 new workers by 2025. However, the challenge is a global one and it is compounded by the fact that those pockets of battery expertise that exist today are not evenly spread across the globe. Much of the world’s battery knowledge and experience is centered in Asia, with China in particular, leading the way. This represents a significant hurdle given the complications of cultural disparity, language barriers and COVID-related global challenges.
This scale of the issue cannot be overstated. The shortage of battery expertise is currently holding back the transformation from ICE to EV within the automotive sector and, the mission to deliver net zero.
Every major player in the battery ecosystem encounters challenges when sourcing the people with the required expertise. And there are plenty of near-deserted offices at start-up and in-house OEM division levels operating with a skeleton staff because, again, they just cannot get the right people to do the job.
So, how do we solve this?
It’s tempting to say that it is found in three words. As a former British Prime Minister once put it: “Education! Education! Education!” And it’s true, the only way any talent shortage has ever been solved throughout history, be it in agriculture, manufacturing or IT, is by teaching people new skills.
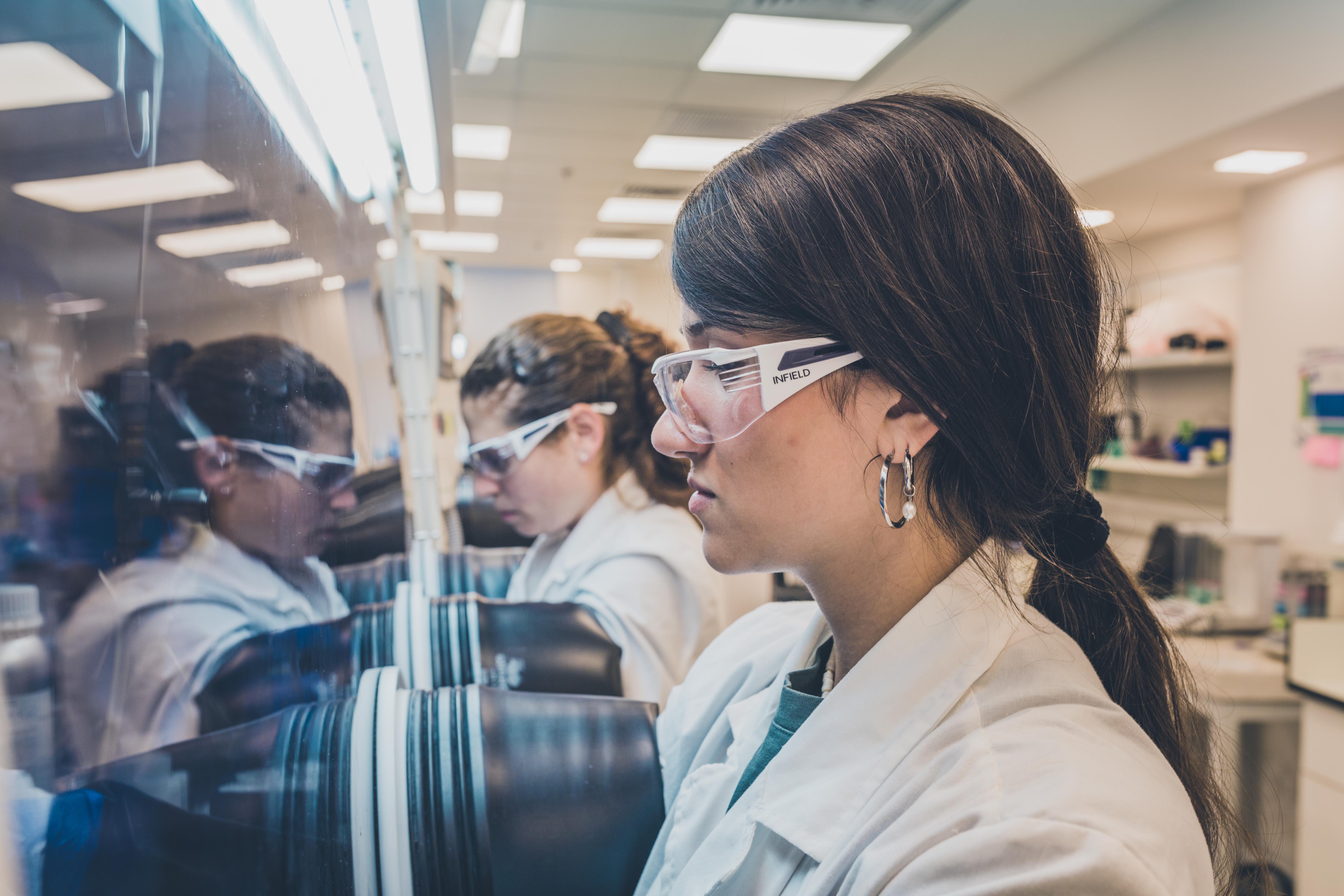
Cohesive solution
But education in isolation alone will not solve the massive challenge the world faces; it must come with co-ordination. Countries, governments, automotive OEMs, and start-ups, plus battery manufacturers, smart city and smart grid developers, infrastructure and charging point providers and universities, technical colleges and schools must come together if we are going to forge the holistic strategies required to ensure the battery-powered transformation to sustainability is delivered.
We also need more initiatives to bridge the gap between knowledge and application, particularly at graduate level. And by that, I mean programs to help those with a degree in chemistry to transfer to electrochemistry to focus on fast-tracking advanced battery development. Culture change on a global scale is equally vital to ensure the acceleration of innovative technology at an ultra-fast pace.
We launched StoreDot in Israel in 2012. Last year we announced our vision by which our extreme-fast charging EV batteries will deliver 100 miles range in 5 minutes of charging by 2024, 100 miles in 3 by 2028 and 100 in 2 within a decade. Having already provided a live public demonstration of our ability to charge 100 miles in 5 minutes, and with our silicon-dominant battery technology undergoing tests with automotive OEMs globally, we are firmly on target to achieve our goals.
At the moment, Israel does not have a significant manufacturing base. But it does have a culture that promotes technology, knowledge, and innovation. In 2009, the Israeli Ministries of Education and Environmental Protection initiated a joint program to implement the concept of sustainability in the education system - from preschool to high school. In addition to highlighting the challenges the world faces from climate change, air pollution, and greenhouse gas emissions, the national education program focuses on the promotion of alternative energies. In addition, Tel Aviv, Bar Ilan and Technion universities all offer programs in electro-chemistry.
There are positive programs running in the UK, too. The University of Warwick offers ‘Battery School’ and ‘Electric Drivetrain School’ learning sessions and provides courses in Battery Systems and Manufacturing. Germany offers similar initiatives, having opened a new research center for battery fabrication last year as part of the Fraunhofer Institute for Production Technology in Munster. In France, a cross-sector consortium opened a battery school in September, which will prove essential to help train the 40,000 battery specialists the country will require by the end of the decade.
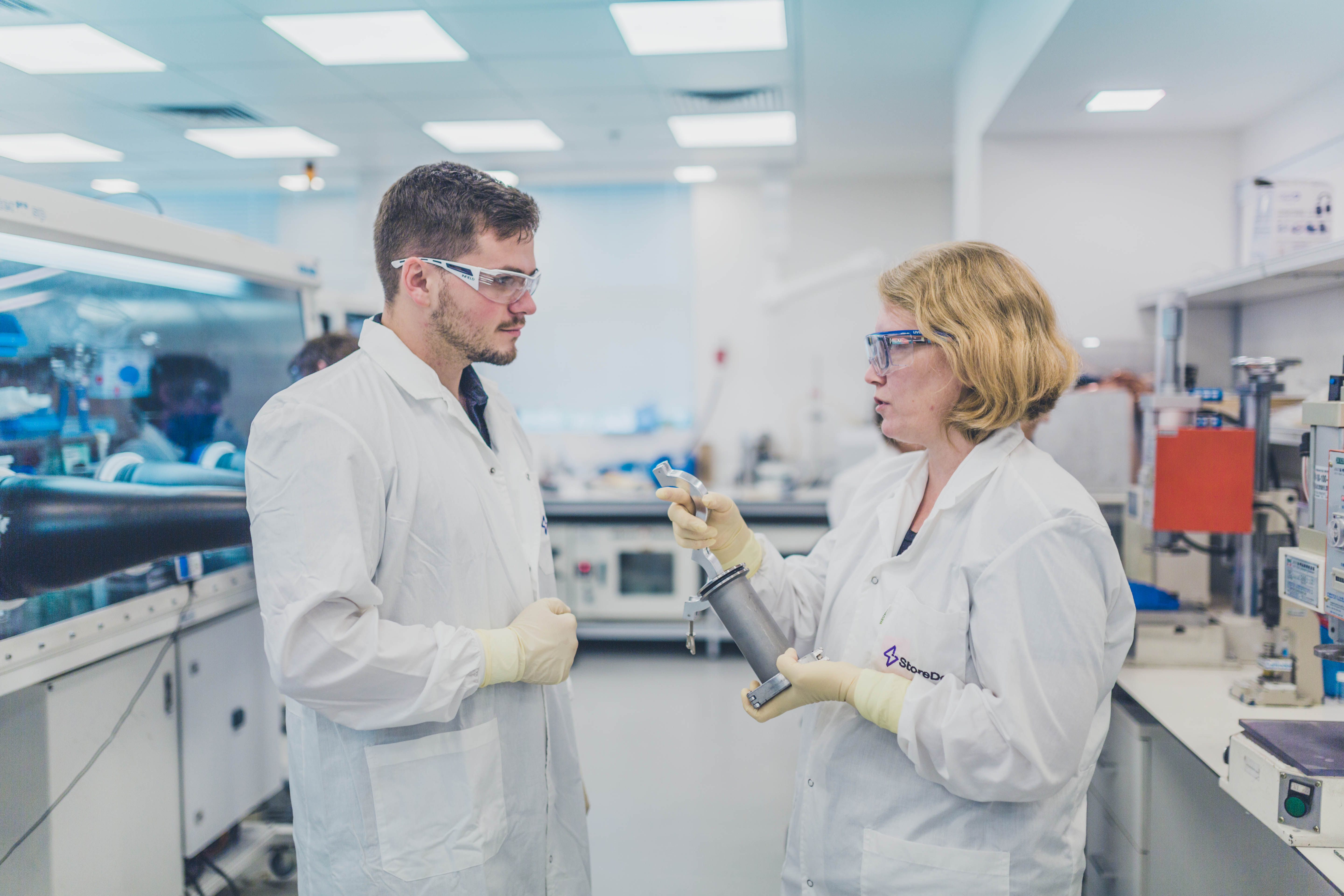
Pro-active response
At StoreDot, we strongly believe it is our responsibility to take a proactive approach to help solve the skills shortage issue. Engaging with the next generation is vital. That’s why we initiated a collaborative educational program with MIT (Massachusetts Institute of Technology, US) and are discussing further initiatives with other universities. At a local level, bringing graduates and school students in to see our laboratories and meet our researchers serves as another useful tool.
But there just isn’t time to wait for the next generation of scientists and engineers to be fully trained to deliver cutting-edge battery solutions that the world needs now. Research and development must continue at as fast a pace as possible. StoreDot was the first company to introduce Agile methodologies, traditionally deployed within software development, to battery development. And we’ve taken a similar pioneering approach to the deployment of AI and machine learning in the development phase of battery technology. Such practices enable us to overcome the traditional limitations that impede startups and serve as a force multiplier for our resources enabling us to be highly competitive in the race to develop next-generation EV battery technology.
We share much of what we learn from these highly effective disruptive strategies. We share it for the wider benefit of the industry not just through publications and the provision of ongoing realistic view of technology readiness, but also by offering some of our patents in an open-source format. That way, the entire ecosystem can benefit from faster time to market. Finally, the fact that we work intensively to become global is also a major contributory factor to solving the challenge of local talent on a global scale and accelerating the journey to sustainable mobility.
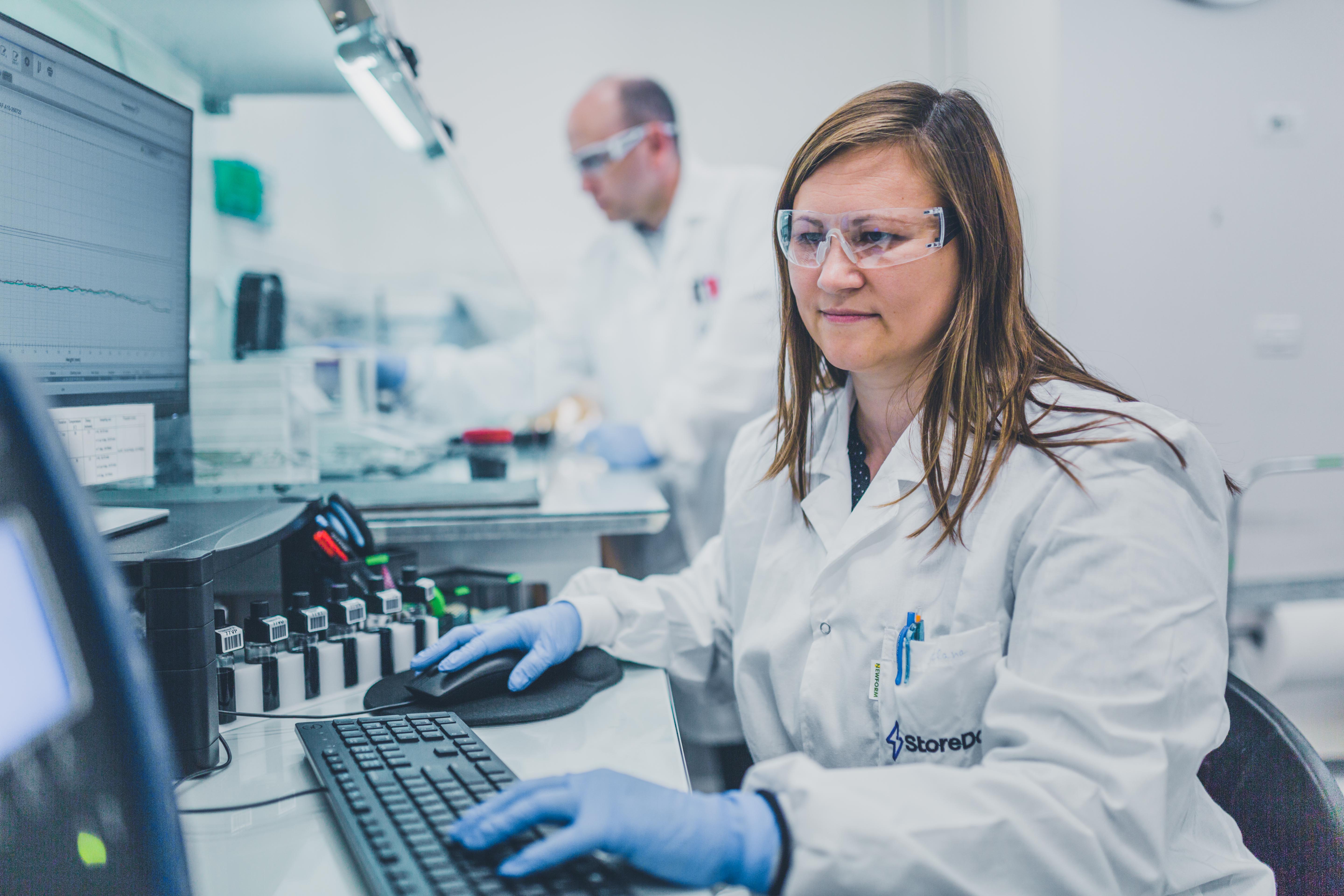
Exceptional opportunity
Preplanning is crucial to facilitate mass adoption of electric vehicles – one of the largest, most impactful revolutions of our lifetime. It cannot be delivered unless governments play a key role by incentivizing educational plans in the battery industry, to complement the efforts being made by setting regulatory carbon-free goals. Urging professionals to obtain the expertise that the battery industry so desperately needs is critical. It must be communicated as a compelling offer for all parties.
For those who forged their careers in the internal combustion era, upskilling to EV technology offers the opportunity to safeguard their jobs and the potential to pass on a better environment to their children and grandchildren.
For those beginning their working life, the possibilities are almost endless. An ongoing process of continuous training and professional development lies ahead in an industry forecast to exceed $420 billion by 2030.
The battery industry is driven by commitment, as people connect to the global mission of our planet and the future generations. The so-called "Quiet Resignation" where employees across various industries only carry out the minimum their roles require is not relevant in this sector.
To secure a successful and sustainable tomorrow, we must initiate a global strategy today that not only solves the current skills shortfall but is also continuously updated and reviewed to avert further challenges in the future.
This article was first published in Electronic Specifier